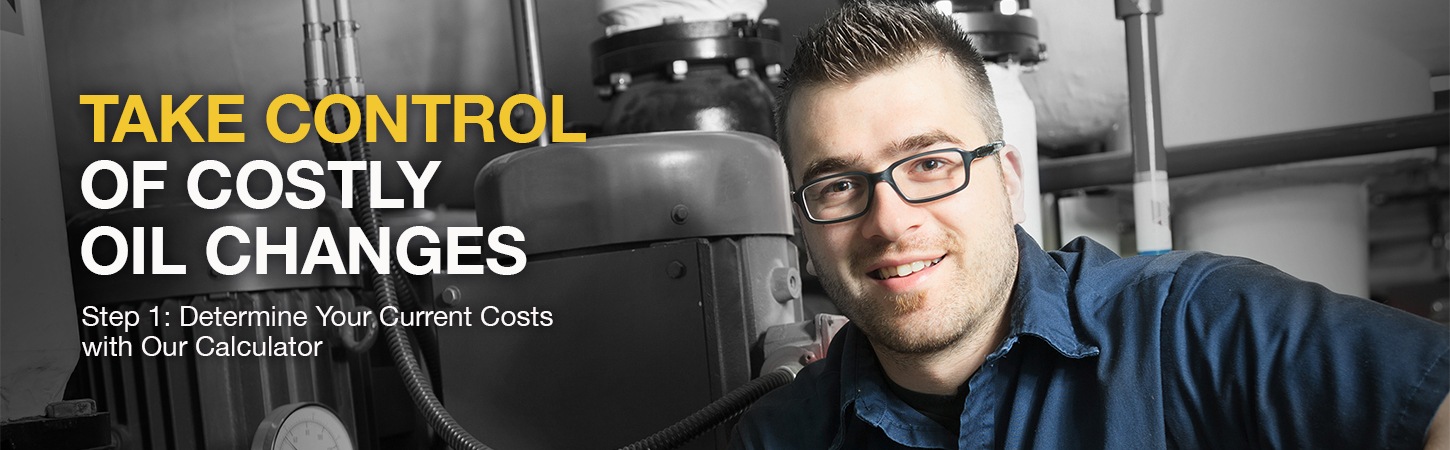.jpg)
Jim Jung
01.14.2020
A Look at the High Upside of Shifting Away from a Routine Preventive Practice to More Predictive Maintenance
Oil changes are a necessary part of anything that uses oil.
Your car, of course, needs oil changes. The rule of thumb used to be changing the oil every 3 months or 3,000 miles to make sure your oil is clean and up to the important job of engine lubrication. Synthetic oils have stretched that rule up to 10,000 miles in some cases.
Increasingly, however, you don’t necessarily have to change the oil based on your odometer. Oil sensors are more prominent now, analyzing the oil to tell you when the right time is for a change. You might use this new insight to reduce annual oil changes, say, from 4 to 2 – saving yourself $100 per year.
That’s a nice, layperson’s example of a key benefit of going from preventive to predictive maintenance. If you only perform maintenance procedures when you need to, based on data and science, you stand to save time and money.
This same opportunity has emerged in our industrial world. Only here, the costs and the potential savings can be eye popping.
Where to Start If You’d Like to Reduce Routine Oil Changes
First, you need to get a handle on the challenge with a bit of benchmarking. Determine the number pumps, gearboxes and hydraulic reservoirs you have and how many oil changes you’re currently doing in a year.
Now, how do you go about increasing the Mean Time Between Oil Changes (MTBOC) – and thereby reducing oil changes and reaping the associated savings?
An oil analysis program is essential to make informed decisions on when and why you should change the oil. What if you found out that many of your scheduled oil changes weren’t even necessary? What if your oil changes are doing more harm than good by replacing what was perfectly good oil with oil that’s in worse condition?
Without oil analysis, you’re flying blind to these possibilities. If you don’t currently do oil analysis, you can try a free sample oil analysis from Trico.
Depending on what your comprehensive oil analysis shows, you may need to make some changes in your lubrication practices to increase your MTBOC. Here are a few examples.
- Make sure you’re putting only clean oil in your equipment. Get oil tested upon arrival because it may not be as clean as you think. Filter oil during storage and/or when dispensing into secondary containers.
- Get organized for proper oil sampling, storage, filtration and transfer. Use clean, dedicated, color-coded, secondary oil containers to avoid cross contamination. Here’s more about the oil storage issue.
- Monitor the lubricant throughout its journey. Start oil analysis at each stage to help uncover problems and their real causes.
These changes not only can increase MTBOC, but also can deliver cost savings that go straight to the bottom line. Not to mention freeing up employees to focus on more value-added activities. Identifying major costs associated with doing oil changes is the first step in cost justification of these key improvements – and we can help with that.
See the True Costs of Critical Equipment Oil Changes
Contact Trico we can help you see how much you’re actually spending.