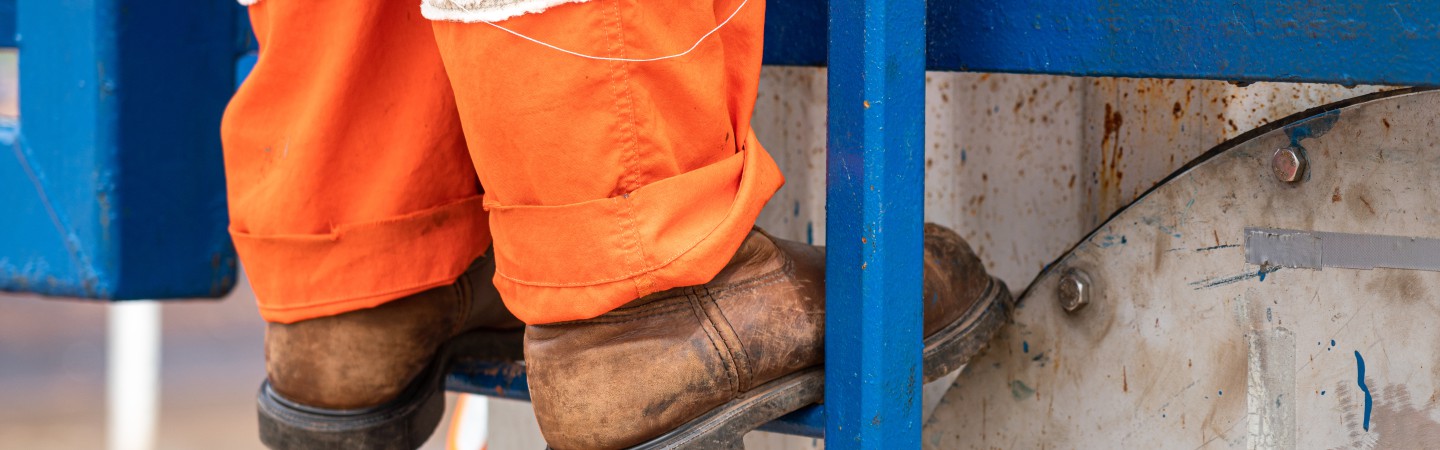
Dan Freeland
11.12.2024
How Real-Time Monitoring Solutions Like Machine Vitals Make a Difference
When it comes to industrial settings, safety isn’t just a guideline; it’s a daily imperative. It's not just a corporate statistical obligation, but a moral obligation as well. Workers face serious hazards, especially during manual inspections where they’re exposed to high temperatures, fast-moving parts, and hard-to-reach equipment areas. Traditional safety inspections, while crucial, involve risks that could be minimized through smarter approaches. Machine Vitals offers a safer alternative by providing real-time monitoring, allowing workers to focus on maintaining safe, productive environments while machines keep a close eye on equipment health.
The High Stakes of Safety in Industrial Operations
Industrial facilities—from manufacturing plants to power generation sites—are filled with hazards that make workplace safety a complex challenge. Consider the risks inspectors face: high temperatures that can cause burns, oily or wet surfaces that make slips a constant threat, and loud machinery that drowns out communication. Often, the equipment is located in cramped, elevated, or isolated spaces, making it dangerous and difficult for inspectors to access. When workers need to gather hands-on data from machinery, they may also encounter rotating parts, electrical systems, and components under pressure. These risks add up, making manual inspections hazardous tasks that deserve a better, safer approach. By leveraging real-time monitoring technology like Machine Vitals, companies can reduce the need for frequent manual checks, keeping workers safe and providing round-the-clock vigilance. This approach not only minimizes physical risks but also offers a more reliable way to spot potential hazards before they lead to equipment failures or accidents.
Real-World Consequences of Equipment Failure
Industrial equipment failures can lead to costly downtime, severe accidents, and sometimes even fatalities. They can become a fire hazard if given the proper conditions. Friction between moving parts, overheating, thermal runaway, and metal-to-metal contact are all catalysts that can result in serious consequences. These conditions underscore the need for continuous monitoring to prevent such breakdowns from happening in the first place. By detecting warning signs like vibration spikes or temperature increases, Machine Vitals can alert maintenance teams to developing issues, allowing them to act quickly and avoid catastrophic failures.
How Machine Vitals Works to Improve Safety
Machine Vitals operates as an automated guardian for industrial equipment, monitoring critical parameters—pressure, temperature, vibration, and more—to keep equipment health in check. Its sensors continually measure these variables, alerting operators immediately when values exceed safe thresholds. Rather than waiting for periodic time-based inspections, maintenance teams receive real-time insights, reducing the time that equipment spends in potentially unsafe conditions. The continuous data gathered by Machine Vitals doesn’t just prevent equipment failure; it provides critical safety alerts in near real-time. For example, if a bearing starts to overheat, the system will immediately notify the team, allowing them to prevent potential explosions or fires. By providing constant feedback on equipment status, Machine Vitals helps mitigate risks and safeguards the people who work near these machines.
Moving Beyond Manual Inspections: The Benefits of Real-Time Monitoring
By reducing the need for physical inspections, real-time monitoring offers substantial safety improvements. Manual inspections require workers to access equipment in high, cramped, or otherwise hazardous locations. Navigating the facility to reach these machines involves long walks across potentially slippery, uneven floors, increasing the risk of falls. Climbing ladders, working around hot machinery, and handling sensors in active areas are just a few examples of the risks maintenance teams face. Reducing the frequency of these inspections can make a huge difference in worker safety. With Machine Vitals, inspections can become a safer and more automated process. Teams can assess equipment conditions remotely and receive instant alerts whenever a critical parameter is breached, allowing them to respond without directly entering high-risk zones. Or, at the very least, provides valuable insights to potentially dangerous conditions before having to inspect what is creating the alert in the first place. This approach saves time and minimizes the physical demands on employees while providing a safer, more intelligent, and more efficient way to monitor equipment.
The Lasting Impact of Machine Vitals on Industrial Safety
The adoption of real-time monitoring technology not only enhances immediate safety but also leads to long-term benefits. Fewer workplace accidents mean a healthier work environment, where employees feel secure and valued. Moreover, real-time monitoring helps facilities comply with safety regulations, reducing the legal and financial risks associated with workplace accidents. Additionally, by preventing unexpected equipment failures, companies can reduce costly downtime and improve productivity. Continuous monitoring extends the lifespan of critical equipment, catching problems early and reducing wear and tear. Over time, these efficiency gains translate to lower repair and replacement costs, adding significant value for businesses. Machine Vitals delivers on both safety and performance, creating a win-win for companies looking to protect both their employees and their bottom line.