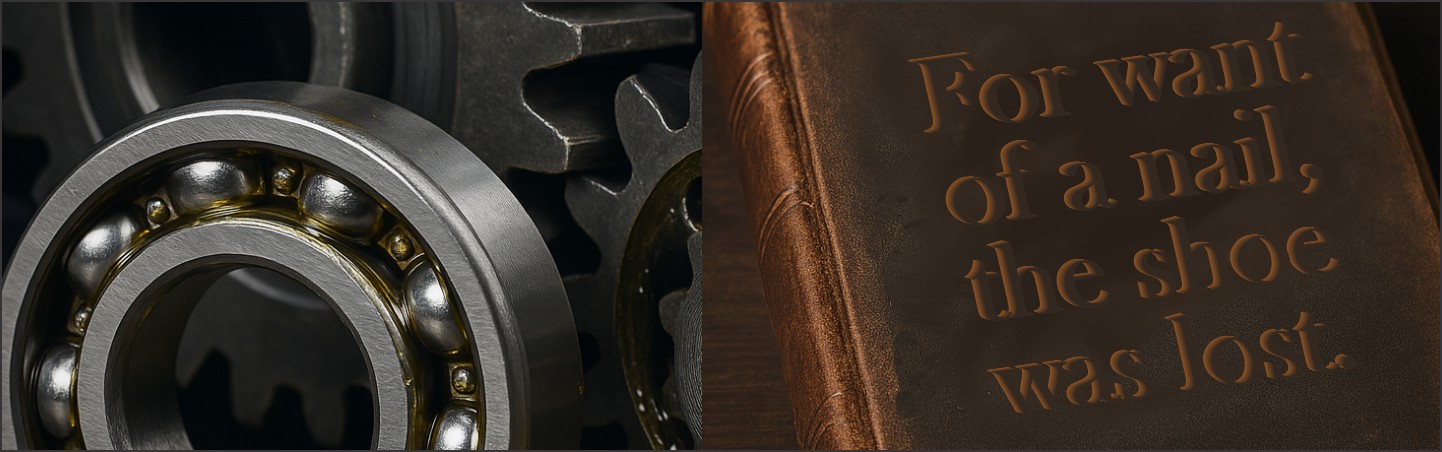
Lisa Kiepert
04.01.2025
Small Things Done Right
“For want of a nail, the shoe was lost…”“An ounce of prevention is worth a pound of cure.”
“Don’t spoil the ship for a ha’p’orth of tar.”
These sayings may have originated in entirely different contexts, but they perfectly capture the value of proper lubrication. Because when it comes to keeping equipment running reliably, it’s often the small things that make the biggest difference.
Lubrication doesn’t usually get the spotlight. but neglecting it leads to unplanned downtime, increased maintenance costs, and avoidable failures. Here’s how the wisdom of old sayings applies directly to modern lubrication management.
1. “The devil is in the details.”
Lubrication is all about precision. It’s not just what’s applied but how, when, where, and in what amount.
- Using the wrong viscosity? Increased wear.
- Dirty transfer containers? Contamination.
- Unlabeled or mislabeled drums? The wrong oil in the wrong machine.
2. “A stitch in time saves nine.”
Small problems become big ones when ignored. That’s the principle behind condition-based lubrication.With tools like:
- Oil analysis
- Vibration, temperature, pressure, and humidity monitoring
- Ultrasonic monitoring
3. “You can’t manage what you don’t measure.” — Peter Drucker
Lubrication programs improve dramatically when they're guided by data instead of guesswork.Measuring lubricant condition, application frequency, and contamination levels helps teams:
- Predict failures
- Improve PM intervals
- Justify decisions with data
- Extend asset life
4. “It’s the little foxes that spoil the vine.”
Many lubrication-related failures aren’t the result of catastrophic mistakes they’re caused by minor issues repeated over time.
- Spent desiccant breathers that need to be replaced
- Lubricant containers left open
- Low oil or grease levels in lubrication devices
- Cross-contamination from reused funnels or tools
5. “Don’t put off until tomorrow what you can do today.”
Deferred lubrication is one of the most common and costly maintenance mistakes.Skipping a lube task may not have immediate consequences, but over time, it increases the risk of breakdowns and shortens component life. Proper lubrication is one of the simplest ways to improve reliability, but only if it's done consistently and on time.
Final Thought: “Take care of the pennies, and the pounds will take care of themselves.”
Good lubrication doesn’t require a massive investment but it does require attention to detail, commitment, and a proactive mindset.By treating lubrication as a precision process not an afterthought teams can prevent failures, extend equipment life, and improve uptime across the board.
Whether in maintenance or life, the smallest actions often lead to the biggest outcomes.
- Category:
- Lubrication Program
- Tags:
- Lubricant
- Lubrication Program