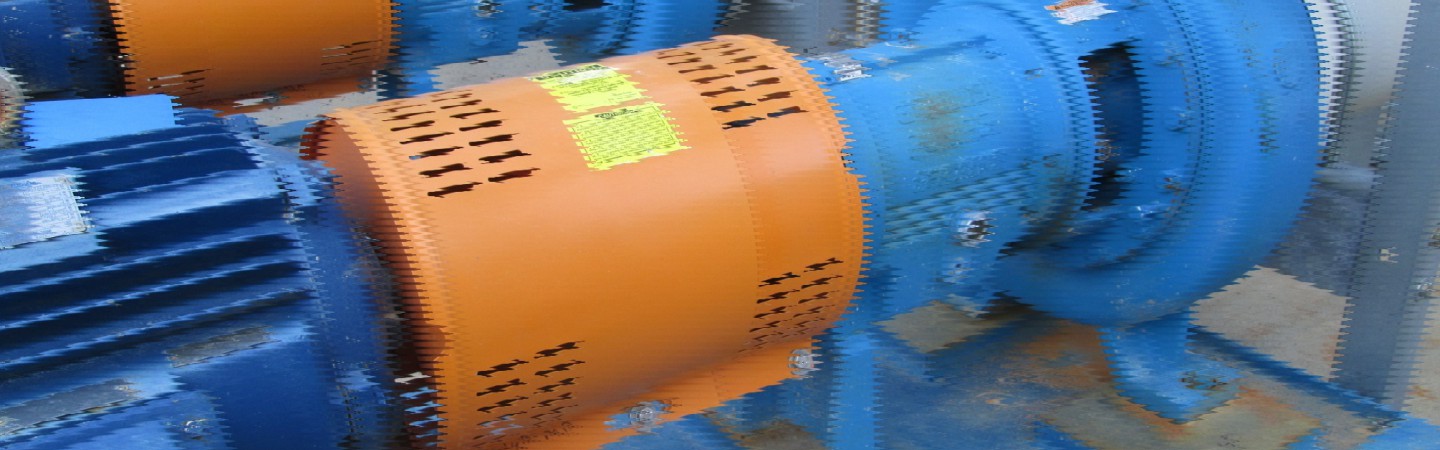
Dan Freeland
02.18.2025
Why Internal Condition Monitoring Gives You More Time on the P-F Curve
For years, vibration sensors have been the go-to tool for detecting mechanical faults in industrial equipment. And while they serve their purpose, helping maintenance teams catch bearing failures before a catastrophic breakdown they come with serious limitations. Vibration monitoring often tells you that something is already wrong rather than giving you a meaningful warning beforehand.Enter “internal” condition monitoring, a more holistic approach to machinery health that doesn’t just wait for failure symptoms to show up but detects the root causes before they turn into real problems. A system like Machine Vitals doesn’t just listen for vibration anomalies; it monitors the conditions inside the bearing housing, gearbox, or hydraulic reservoir long before vibration even becomes an issue.
The Limits of Vibration Sensing
A vibration sensor is like a smoke detector in your house: it warns you when there's already a fire. By the time increased vibration is noticeable, damage to a bearing, gear tooth, or pump shaft is often well underway. This is where the P-F curve, the timeline from Potential Failure (P) to Functional Failure (F), becomes important. Vibration sensing usually picks up failures when they are already in progress, meaning you're closer to the "F" (functional failure) end of the curve than you'd like. Small defects in bearings or misalignments in shafts might go unnoticed until they start to resonate as vibration. But by that time, the damage has begun, and maintenance options are limited to either shutting down the equipment for repairs or running it until failure.
A Better Approach: Monitoring the Housing Environment
A system like Machine Vitals changes the game by monitoring internal conditions that lead to failure well before vibration becomes detectable. Instead of just reacting to damage, it watches for the conditions that cause damage in the first place. Take lubrication issues, for example. Most bearing and gearbox failures are due to contaminated or degraded oil, leading to increased friction, heat, and eventually mechanical wear. Traditional vibration monitoring doesn’t tell you that your lubricant is slowly breaking down, but Machine Vitals does. By tracking oil headspace pressure, temperature, humidity, and airborne contaminants, it detects early warning signs of oil degradation or water ingress that, if left unchecked, will eventually lead to increased vibration.
Imagine a slow rise in headspace relative humidity. This could indicate water ingress, which means the oil's additive package will start breaking down sooner. A vibration sensor won’t detect this until the bearings start to pit and spall. But with early detection, maintenance teams can change the oil or dry out the system long before the damage begins, keeping the equipment in top shape rather than reacting after the fact.
No Other Product Provides These Insights
No other product in the world provides this level of insight. While traditional monitoring tools detect failures only after damage begins, Machine Vitals offers an unmatched ability to identify issues before mechanical wear even starts—giving maintenance teams weeks or even months of advance notice. By shifting detection further left on the P-F curve, Machine Vitals empowers teams to take proactive action, reduce downtime, and extend the life of critical assets.
Where Do These Technologies Sit on the P-F Curve?
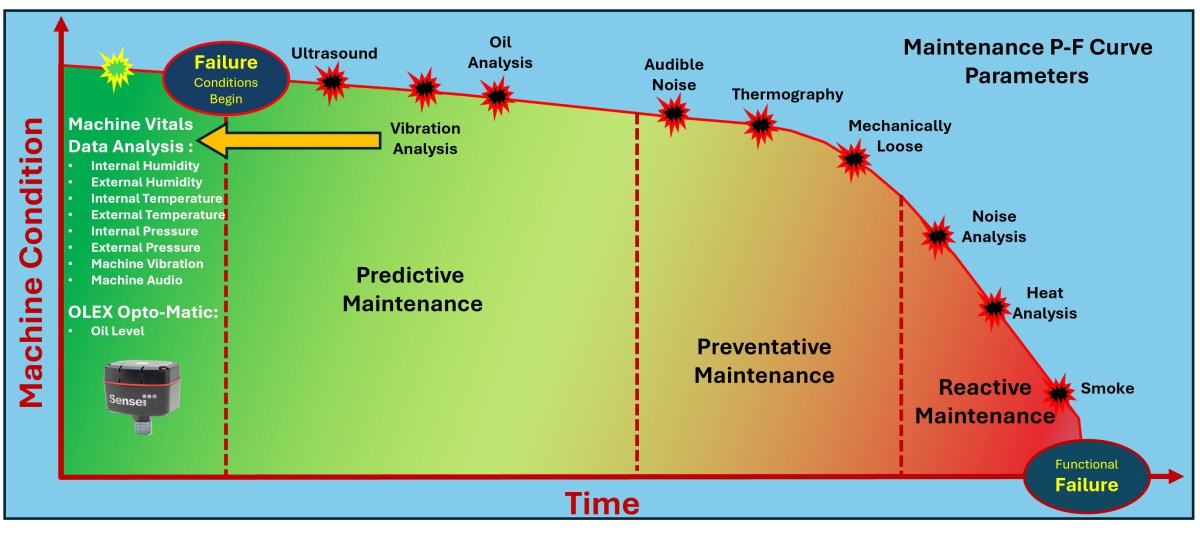
Vibration monitoring only detects failures once they're already causing mechanical symptoms, meaning you're often just a short time away from the failure event. Machine Vitals, on the other hand, moves your detection point much earlier—closer to the "P" (Potential Failure) mark—giving you weeks or even months of advanced warning.
How Machine Vitals Prevents Future Vibration Issues
Not only does Machine Vitals detect problems early, but it also prevents future vibration issues before they even start. Here’s how:
- Lubrication Problems → Increased Friction → Bearing Wear → Vibration
- Water Ingress → Oil Breakdown → Corrosion & Pitting → Vibration
- Pressure & Temperature Changes → Cavitation & Aeration → Gear Damage → Vibration
The Payoff: Extending Equipment Life
The real benefit? A dramatic increase in equipment lifespan. Studies show that proactive maintenance can extend machine life by 20-40% compared to reactive maintenance. Since Machine Vitals moves your failure detection further left on the P-F curve, it doesn’t just help you catch issues earlier, it reduces the frequency of those issues occurring in the first place.
Final Thought: Do You Want a Fire Alarm or a Fire Prevention System?
Vibration sensors are still useful, but they’re only part of the picture. If you want to move beyond reactive maintenance and extend the life of your equipment, you need a solution that tells you what’s happening inside the system—not just when it starts making noise. Machine Vitals does exactly that. Instead of waiting for vibration to signal a problem that’s already underway, it monitors the conditions that lead to failure, giving you more time to act and keeping your machines running longer.
Which would you rather have? A last-minute warning, or a chance to prevent the failure altogether?