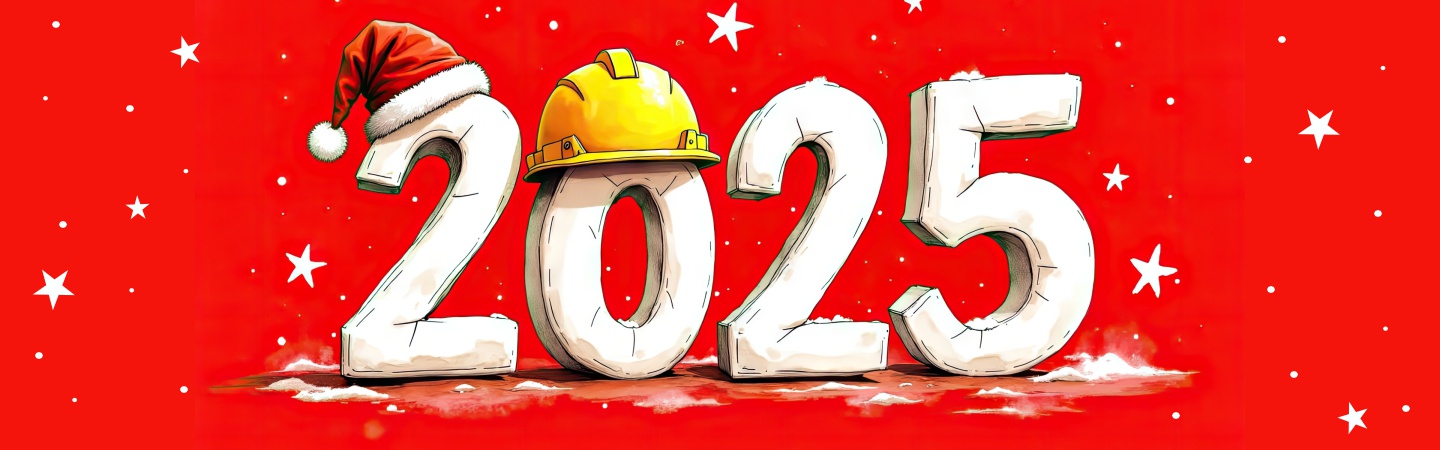
Lisa Kiepert
12.17.2024
Optimizing Your Lubrication Practices
As 2025 approaches, it’s the perfect time to evaluate your lubrication practices and set the stage for a year of reliability and efficiency. A robust lubrication management program not only minimizes downtime but also drives operational excellence and extends equipment life. Here’s how to ensure your new year starts on a strong note:
1. Audit Your Lube Room
Is your lube room an asset or an after-thought? A clean, organized, and properly stocked lube room reduces the chances of cross-contamination, ensures easy access to the right lubricants, and boosts efficiency. Start the year by auditing your lubricant storage and handling:• Are lubricants stored in labeled, sealed containers?
• Are desiccant breathers in place to keep contaminants out?
• Is the layout optimized for easy navigation?
2. Reevaluate Your Lubrication Products
Not all lubricants are created equal, and what worked last year might not be optimal now. Changes in machinery, workloads, or operating environments might call for a reassessment:• Are you using the right viscosity grades?
• Are your suppliers providing clear, up-to-date specifications?
3. Implement Condition Monitoring Tools
Don’t rely on guesswork. Advanced condition monitoring tools can give you real-time insights into the health of your lubricants and equipment:• Oil Analysis: Identify contamination, wear particles, and degradation early.
• Sensors: Deploy devices like the Sensei Family of condition monitoring sensors for relative humidity, vibration, and temperature tracking.
• Automated Alerts: Set thresholds to trigger alerts, enabling quick responses to potential issues.
4. Focus on Training and Education
Even the best tools are only as effective as the people using them. Kick off 2025 by ensuring your team is equipped with the knowledge they need:• Offer refresher courses on lubrication best practices.
• Train staff on new technologies and tools.
• Share success stories to foster a culture of continuous improvement.
5. Adopt Proactive Maintenance Strategies
A reactive approach to maintenance is costly and inefficient. This year, commit to a more proactive strategy:• Schedule regular lubrication checks.
• Use predictive analytics to anticipate potential failures.
• Document all maintenance activities to refine your processes over time.
6. Measure Success
You can’t improve what you don’t measure. Establish key performance indicators (KPIs) for your lubrication program:• Lubricant consumption rates.
• Mean time between failures (MTBF).
• Equipment downtime linked to lubrication issues.
The Payoff: Efficiency, Reliability, and Savings
Effective lubrication management is about more than preventing breakdowns. It’s a driver of operational excellence, cost savings, and sustainability. By taking a structured approach to lubrication management in 2025, you’ll not only reduce unplanned downtime but also extend the life of your equipment and improve overall productivity.
Ready to Elevate Your Lubrication Game?
2025 is the year to make lubrication management a strategic priority. Whether you’re starting fresh or refining an existing program, we are here to help guide you toward a smoother, more reliable year ahead.- Category:
- Lubrication Program