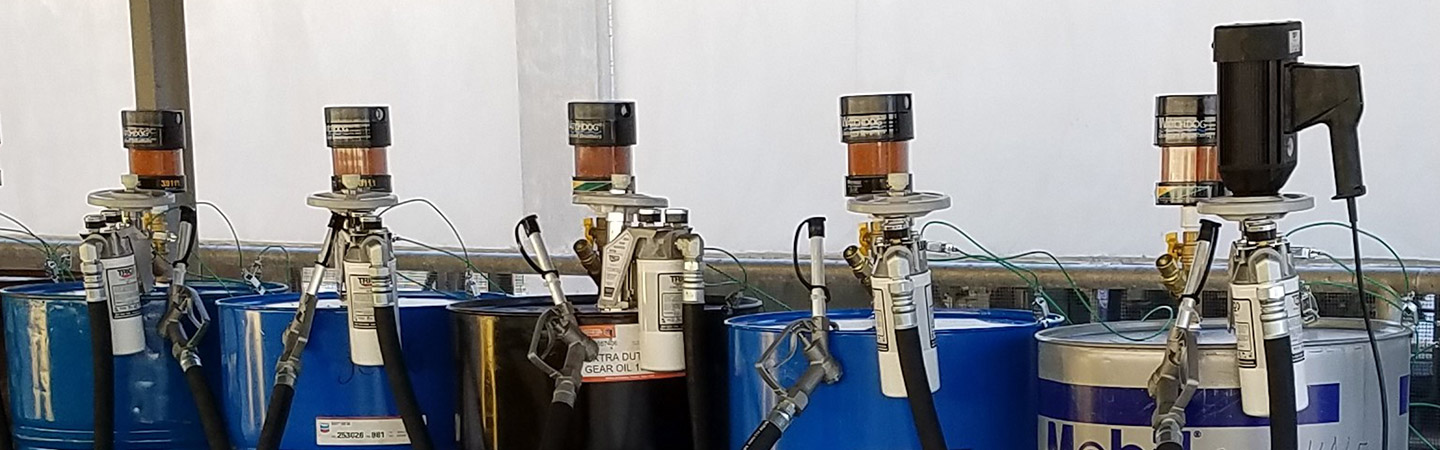_1.jpg)
Mike Gauthier
12.03.2019
A Well-Organized Lube Room Helps Protects Your Critical Equipment and Your Team. Follow These Steps to Start Storing Smarter.
We get it.
With everything else on your mind, you may not spend much time worrying about how and where you store equipment lubricants.
But really, you should. Because oil is the lifeblood of your equipment, storing your lubricants properly is just as important as effectively maintaining any critical asset in your plant.
If you need further convincing, imagine you’re in a car accident. You’re rushed to the emergency room, in need of a blood transfusion to survive. If the blood bank your life-saving blood came from looked anything like your lubricant storage, do you think you’d survive?
Neither will your equipment!
A haphazard approach to oil storage leads to:
- Time wasted tracking down and handling lubricants
- Safety threats due to spills and poor handling
- Equipment damage and downtime caused by using contaminated, degraded or flat-out-wrong lubricants
On the flip side, investing the resources to create a world-class lube room pays hard and soft dividends – increasing productivity, safety and mean time between failures (MTBF).
Here is a high-level roadmap to help you start storing smarter.
1. Take stock and consolidate if you can.
First, you need to figure out how much storage room you need.
Assess required lubricants based on equipment type, application and environment. Eliminate lubricants you don’t use. You may be able to consolidate products if you find the same formulation from different manufacturers.
After that, determine how much of each oil you should keep on hand, based on amounts used, purchase frequency, shelf life and price. At that point, you can think about the storage strategy and types of containers that will work best.
You can learn more about oil storage container options on Trico’s website.
2. Establish your storage location.
You’re looking for a space that’s clean, dry, temperature and humidity controlled if possible, and big enough to store all lubricants and accessories.
Not enough internal space? Try increasing planned inventory turns and purchase lower volumes at higher frequencies. If you still don’t have enough room, you may need to plan and budget more to build climate-controlled external storage.
The reason a climate-controlled space is so important is because you need to …
3. Control contamination.
Heat and humidity create moisture inside oil containers, and that water ends up in the lubricant. If you don’t think that’s a problem, consider that as little as 1% water in oil can reduce the life expectancy of a journal bearing by as much as 90%. If you think that sealed barrels are preventing the ingression of moisture, consider the barometric pressure changes the barrels incur naturally or their exposure to temperature changes causing expansion and contraction. They will breathe no matter what!
Dirty, dusty areas area not ideal for storage, either. Where products such as cement dust and coal dust are in the air, ultimately the particulate ends up in the containers and the oil.
Which isn’t good because about 82% of mechanical wear is caused by particle contamination, and keeping oil at or under its relative ISO code can result in 3-4 times component life.
What Goes Wrong When Contaminants Get in Your Oil ?
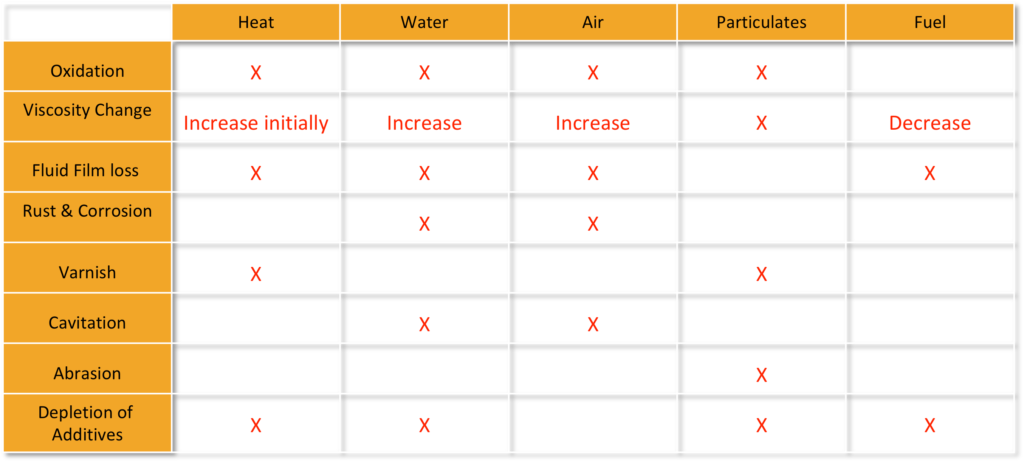
Essential components of controlling contamination of stored oil include:
- Filtration systems when dispensing from the storage containers.
- Desiccant breathers on all stored oil drums to let the containers breathe and control moisture.
- Disposable fast funnels in place of the typical, contamination-friendly plastic or metal ones.
4. Organize and label.
This stage is crucial for preventing cross-contamination of lubricants throughout their life cycle.
Differentiate lubricants by color, using this color for all storage containers, filter equipment, secondary containers and ID tags at the point of use. Create large posters for which lubricant = which color.
If possible, mark your storage area with anti-slip floor paint. Label floor locations, storage containers and secondary containers with contents.
5. Establish clear practices.
So now you have a clean, well-organized lube room. Does your team know what to do with this great new asset?
Create Standard Operating Procedures (SOPs) for all lubricant handling activities related to each piece of equipment, so that everyone consistently uses the right product in the right way.
SOPs should include date stamping new oil and labeling first use to monitor shelf life and facilitate FIFO (First-In / First-Out) stock management. In addition, be sure to establish and train your team on safety practices for spill containment and fire suppression in and around the space.
Finally, to help maintain the advantage of your gleaming new lube room, implement a 5-S program in the lube storage area: Sort, straighten, shine, standardize, sustain. Assign specific personnel to be accountable ensuring it remains in showroom condition.
Don’t get overwhelmed. These don’t all need to be done at once, but the more progress you make in following these practices, the more markedly you’ll improve your safety and reliability of plant assets.
- Category:
- Contamination
- Storage