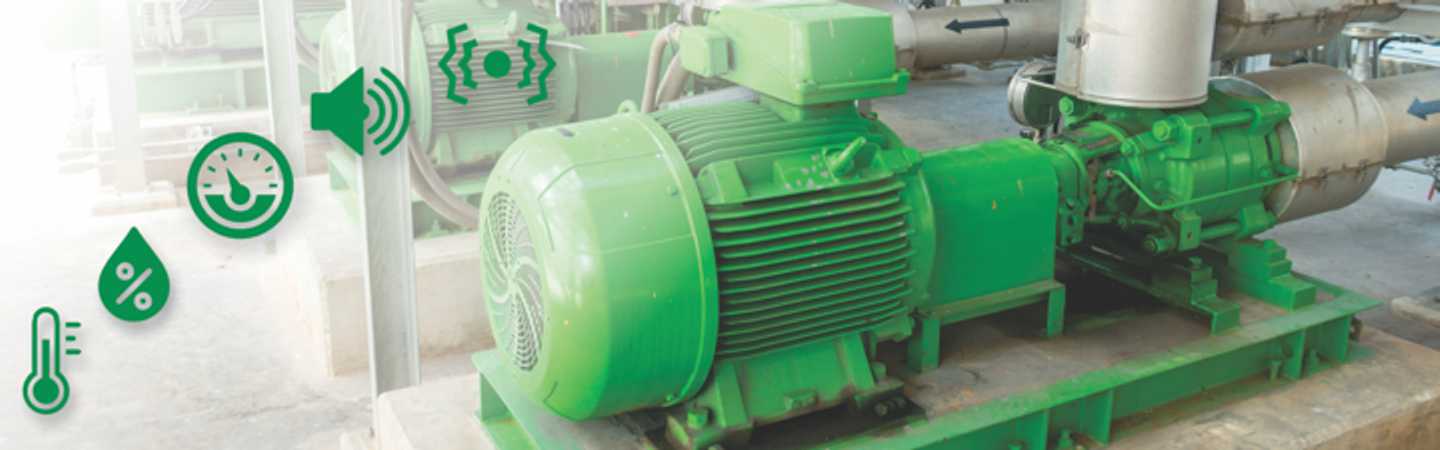
Dan Freeland
01.23.2024
How Industrial Sensors Save Time and Money in Maintenance and Reliability
In the world of maintenance and reliability, bearings and gears are the unsung heroes that keep machines running smoothly. But what happens when these crucial components aren't monitored correctly? The result can be catastrophic failure, leading to lost productivity and costly repairs. That's why it's essential to maintain a "micro-environment" around these components and monitor internal and external environmental factors like temperature, humidity, pressure, and vibration.Industrial sensors are a vital element of modern maintenance and reliability systems. They're designed to monitor the condition of machines, alert operators to potential failures, and provide essential data for predictive maintenance. Sensors can be found in a variety of applications, from temperature probes to accelerometers to pressure transducers. These sensors are particularly crucial in environments where there are small spaces, high temperatures, and challenging conditions to monitor.
Why Are Sensors Important?
Let's explore why sensors are so important in maintaining rotating equipment. Consider a hypothetical scenario where a bearing is running hot. In the past, the only way to detect this issue was through manual monitoring with infrared temperature guns. However, the use of industrial sensors can provide early detection, allowing maintenance personnel to act quickly and prevent more significant damage. By detecting the issue early, the sensor not only saves the machine from premature failure, but it also saves time and money in repairs.
Another essential use of industrial sensors is to detect changes in vibration patterns. When bearings or gears start to fail, they often make more noise and undergo changes in vibration patterns. A machine that's vibrating abnormally could be dangerous, with the risk of parts becoming loose and causing catastrophic failure. By monitoring vibrations, sensors can alert maintenance personnel to these changes and prevent unplanned downtime.
Pressure sensors are also essential in maintaining machines with hydraulic systems. A small pressure differential can cause significant issues with a hydraulic system, leading to inferior performance, leaks, and even failure. By monitoring the pressure differential, industrial sensors can alert maintenance personnel to issues before they escalate, resulting in expensive repairs.
Lastly, humidity sensors are vital for maintaining environments where bearings or gears may be exposed to moisture. High levels of humidity can cause corrosion and premature failure. By using humidity sensors, maintenance personnel can ensure that the environment around rotating equipment is adequately controlled, preventing unnecessary costs and downtime due to corrosion.
When it comes to maintaining rotating equipment, the use of industrial sensors can pay dividends in both time and money saved. By monitoring the micro-environment around bearings and gears, maintenance personnel can prevent catastrophic failures and catch issues before they escalate. Industrial sensors are a critical tool in the maintenance and reliability professional's toolkit. So, invest in good sensors and keep those machines running smoothly!