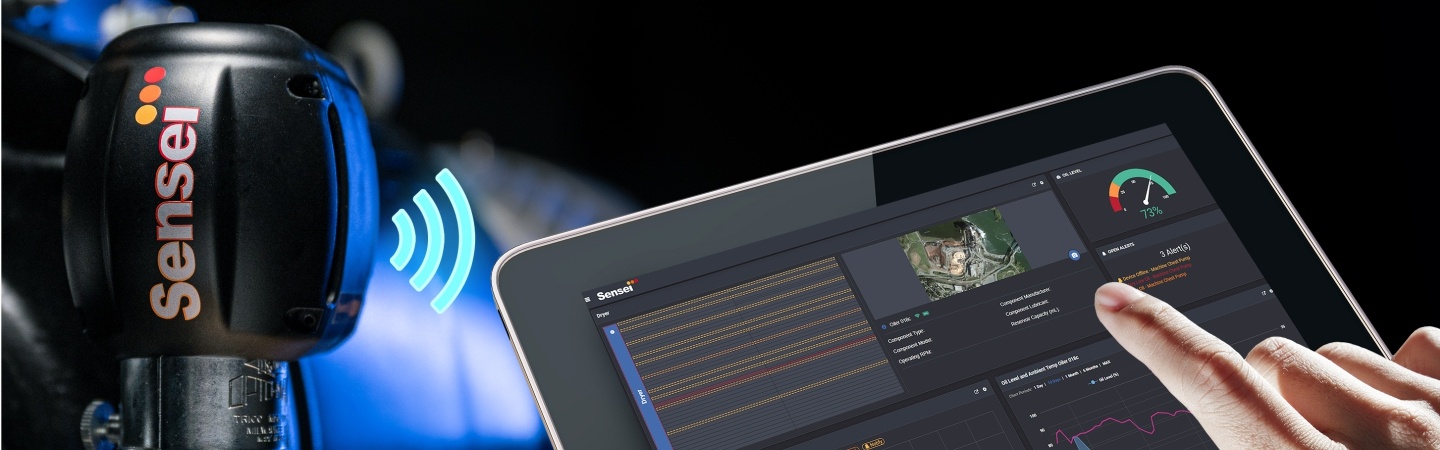
Dan Freeland
06.13.2023
The Key to Preventing Premature Equipment Failure
Maintenance tasks play a crucial role in ensuring the longevity and optimal performance of critical equipment in various industries such as pulp and paper, power generation, chemical processing, and wastewater treatment plants. Although necessary, regular maintenance can also be quite time-consuming and expensive, not to mention the potential for non-value-added maintenance tasks that can lead to premature equipment failure. However, introducing diagnostic sensors on your machines can be a game-changer in identifying and prioritizing maintenance efforts.
What are diagnostic sensors?
Diagnostic sensors are essentially wireless, electronic devices that are mounted on critical equipment that monitor and measure various parameters to detect any changes or abnormalities in their performance. These sensors function as the "eyes and ears" of the equipment and provide real-time feedback on their condition and operational performance.
How do diagnostic sensors help prevent premature equipment failure?
Diagnostic sensors play a crucial role in preventing premature equipment failure by enabling maintenance teams to identify and address issues as they arise, minimizing downtime and reducing the risk of costly repairs or replacements. In particular, diagnostic sensors can detect and alert maintenance teams to potential equipment failures before they occur, allowing them to take proactive measures to mitigate the impact. This approach can significantly reduce equipment downtime, increase productivity, and ultimately save organizations considerable time and money.
How do diagnostic sensors help prioritize maintenance efforts?
One significant challenge facing operations and maintenance managers, particularly in labor-depleted maintenance teams, is prioritizing the maintenance of critical equipment. Limited resources and personnel make it challenging to manage all equipment and address maintenance needs within manageable timelines.
However, diagnostic sensors can help prioritize maintenance efforts by providing critical data on equipment performance, aiding in identifying which machines require immediate attention and focusing maintenance resources where they are most needed. This approach ensures that maintenance teams can make data-driven decisions and optimize scarce resources to prevent unplanned downtime, costly repairs, or potential equipment failure.
What are the benefits of implementing diagnostic sensors?
Implementing diagnostic sensors on critical equipment has numerous benefits for organizations across various industries. Aside from reducing the risks associated with premature equipment failure and prioritizing maintenance efforts, diagnostic sensors can also help:
- Improve equipment reliability and availability
- Reduce maintenance costs and extend equipment life
- Enhance safety and mitigate risks to personnel and the environment
- Improve overall plant performance and efficiency
What should organizations consider in implementing diagnostic sensors?
To ensure the successful implementation of diagnostic sensors in their maintenance programs, organizations must consider several factors. These include, but are not limited to:
- Identifying critical equipment to be monitored
- Determining which measurements and parameters to monitor
- Selecting the appropriate sensors for each application
- Establishing a monitoring and maintenance schedule
- Training and providing support for maintenance personnel
Overall, diagnostic sensors have proven to be an invaluable tool in preventing premature equipment failure and optimizing maintenance efforts in various industries. By providing real-time data on equipment performance and condition, diagnostic sensors enable organizations to prioritize maintenance efforts, minimize downtime, extend equipment life, and improve overall plant performance. As such, organizations must consider implementing diagnostic sensors in their maintenance programs while ensuring that they take a data-driven, systematic approach to achieve the optimal benefits.