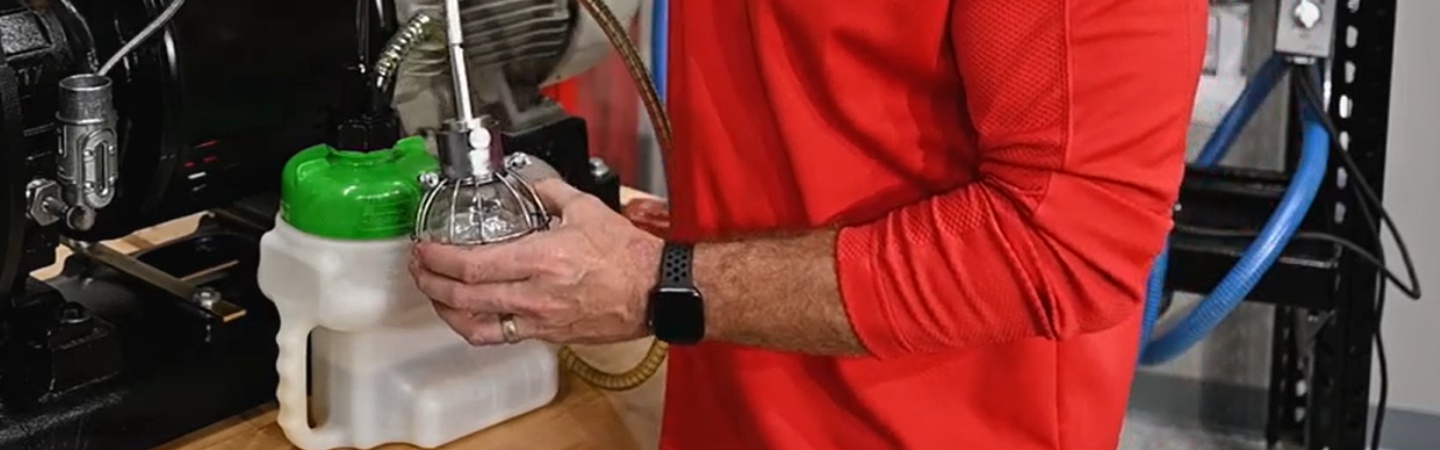
Dan Freeland
10.29.2024
Old School Routine Meets High Tech Smarts
If you’ve ever worked in a facility with industrial rotating equipment, you’ve probably heard of lube routes. No, it’s not a scenic drive through the oil fields—it’s the traditional maintenance process where technicians dutifully make their rounds, lubricating every piece of equipment in sight. These routes ensure that machinery like pumps, motors, conveyors, and gearboxes are kept smooth and operational, avoiding costly breakdowns. But with all the buzz around predictive maintenance, smart sensors, and data-driven decision-making, you might be wondering: are lube routes still a thing in today’s high-tech world?Spoiler alert: Yes, they are—but they’re evolving.
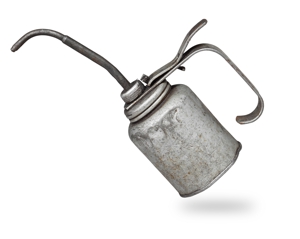
In their most basic form, lube routes are a systematic maintenance schedule. Think of it as a weekly (or monthly) oil change but for an entire facility. A technician follows a set path, hitting all the necessary points, and applying grease, oil, or whatever the machinery requires. It’s preventive maintenance 101: you keep lubricating things at regular intervals, preventing wear, overheating, or worse a complete equipment failure.
For decades, this approach worked like a charm. Companies relied on fixed intervals recommended by equipment manufacturers, or based on experience, to decide when to grease those bearings or top off the oil. It’s like saying, "I don’t know if my car needs oil yet, but let’s do it now just in case."
This traditional approach works well enough, but it’s not exactly efficient. You might be:
- Over-lubricating: Slathering on more grease than necessary, which could cause damage like bearing failures due to heat buildup.
- Under-lubricating: Missed lube points or waiting too long between intervals, leading to premature wear and tear.
- Missing Early Warning Signs: Lube routes can miss warning signs of bigger issues. Technicians might not notice small increases in temperature or subtle changes in vibration that signal an imminent failure.
Here’s how it works:
- Condition Monitoring: Instead of relying solely on human judgment, sensors like the ones in Machine Vitals are installed on equipment to monitor real-time parameters such as temperature, vibration, and pressure. These sensors give an early heads-up when things are starting to go awry. For example, a temperature spike or change in vibration patterns can tell you that a bearing is getting too hot and might need lubrication before it seizes up.
- Automated Alerts: If something’s not right, the system can ping maintenance teams—whether it’s time to add lubricant (Sensei Enabled Opto-Matic Oiler) or inspect the equipment for more serious problems. This can turn a traditional lube route into a condition-based maintenance route. Instead of visiting each machine on a rigid schedule, you only stop by the ones that need attention. That’s fewer unnecessary stops and less time wasted greasing machinery that’s already in good shape.
- Data-Driven Decisions: Systems like Machine Vitals take it a step further, aggregating data in the cloud and running predictive algorithms to tell you not just when to lubricate, but why. If a gearbox is running hotter than usual under the same load, it could mean lubrication is breaking down or contamination is creeping in. Perhaps an oil sample needs to be taken and analyzed to give you an even better picture. Suddenly, your lube route becomes part of a broader, more intelligent maintenance strategy. Congratulations. You’ve just started performing preventive maintenance.
In many industries, lube routes remain essential because:
- Not all equipment is sensor-enabled: For older or less critical machinery, investing in sensors may not make sense. A technician with a grease gun and a checklist can still get the job done.
- Routine Inspections: During lube routes, maintenance teams can catch more than just lubrication issues. They can listen for strange noises, feel for excessive vibration, and inspect for leaks or other potential problems.
- Condition-Based Stops: Sensors monitor equipment and only trigger maintenance when lubrication is truly needed. The days of blindly following a route for the sake of date-based routines are numbered.
- Integrated Lubrication Management: Digital systems guide technicians, helping them document tasks, receive alerts, and even adjust routes on the fly based on real-time data.
So, in the end, make it the best of both worlds. Lube routes aren't going anywhere, but they’re definitely getting smarter. What used to be a repetitive, one-size-fits-all task is now a more targeted, data-driven operation. Thanks to technology like Sensei Machine Vitals and Sensei Enabled Opto-Matic Oiler, maintenance teams can optimize their routes, making fewer stops, applying just the right amount of lubricant, at the right time, and avoiding breakdowns more effectively than ever before.
In the end, it’s all about efficiency. Whether you’re manually greasing bearings or letting sensors do the thinking, the goal is the same: keep those machines running smoothly. And if you can do that with fewer headaches and better insights? Well, that’s the future of lubrication—one smart, sensor-enhanced route at a time.
Discover how smart sensors and timely interventions keep your equipment performinng efficiently, with less downtime and more insight.