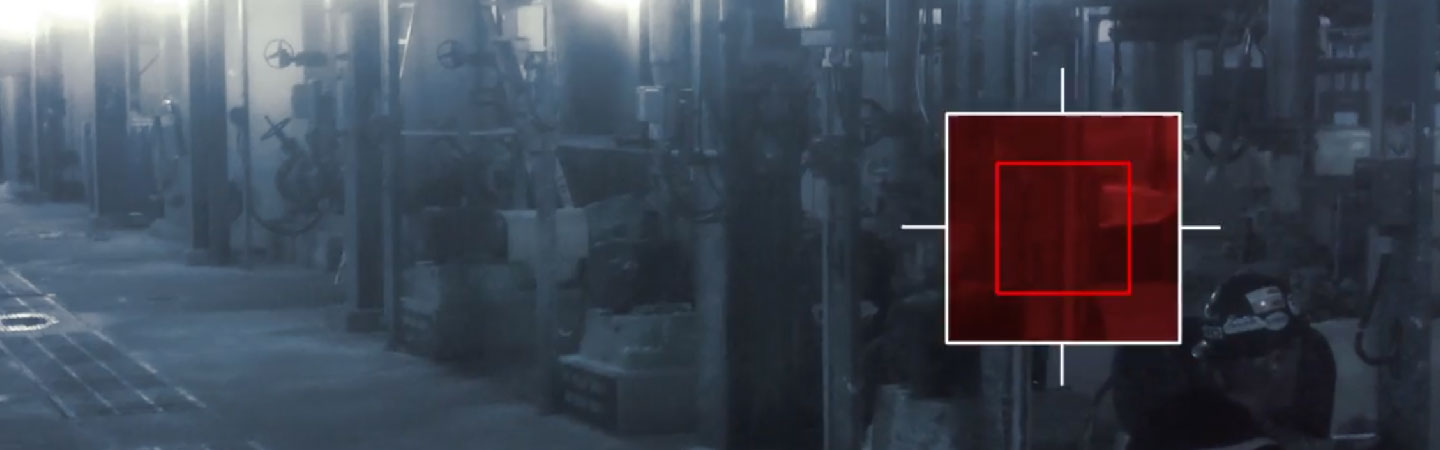
Mike Gauthier
10.15.2019
Data Showed 95% from Oil Contaminated by Water & Particulate
In the hot, harsh environments where boilers help produce power, the threat of water and dirt ingression into boiler feed pumps is undeniable.
When Trico looked at 12 months of oil sampling data from the bearings on boiler feed pumps at three power generation plants, 95% had threateningly high levels of water and particulate contamination.
It’s important to note that contaminants can get into your machinery oil in lots of different ways. How it’s stored and handled in your facility is one big issue, for example.
The issue we’d like to highlight today, however, is the way the boiler feedwater pump itself is set up. See our recommended solution at the bottom, or read on for a closer look at this issue.
Boiler feedwater pumps need to “breathe,” equalizing pressure when air expands and contracts due to temperature fluctuations or startup/shutdown situations.
This breathing allows ingression of moisture and particulates – often in high concentration in the surrounding air – into the oil inside the pump.
What Should You Do to Prevent Contaminant Ingression?
Because contaminants can enter your oil at many different points in your facility, the first thing to do is take samples from different points and have them analyzed to determine if and when oil contamination is occurring.
If expert oil analysis finds that water and particulate are getting into your lubricant at the machine, then the answer is relatively simple: close every possible pathway for the contamination that causes bearing failure, and filter out the rest.
Based on years of working through this issue with many different plants, here’s a setup we might recommend for at-risk boiler pumps.
Closed System Oiler – Ensures that clean, dry oil is always available, offsetting oil loss due to use, leaks or sampling. Read more about closed systems.
Pressure Balancing Line – Equalizes air pressure between the bearing housing and the oiler, eliminating the need for other breathers or vents that allow contaminant ingression.
Desiccant Breather – Filters out moisture and particulates to provide clean, dry air when pressure balancing is necessary in the bearing housing.
Bottom Sediment & Water (BS&W) Bowl – Allows particulate and water to collect at the bottom for easy removal. Includes a viewport to check oil condition as well as an effective sampling location.
Keep in mind, again, that just putting this kit on your pumps won’t necessarily fix all the contamination problems. But plants that have installed this setup have seen some good results, including spotting and avoiding bearing failures before they cause downtime.
Discover the Trico Boiler Feed Pump Protection Kit
Download the PDF below to learn more about a closed system setup that can help you minimize oil contamination and related downtime threats.