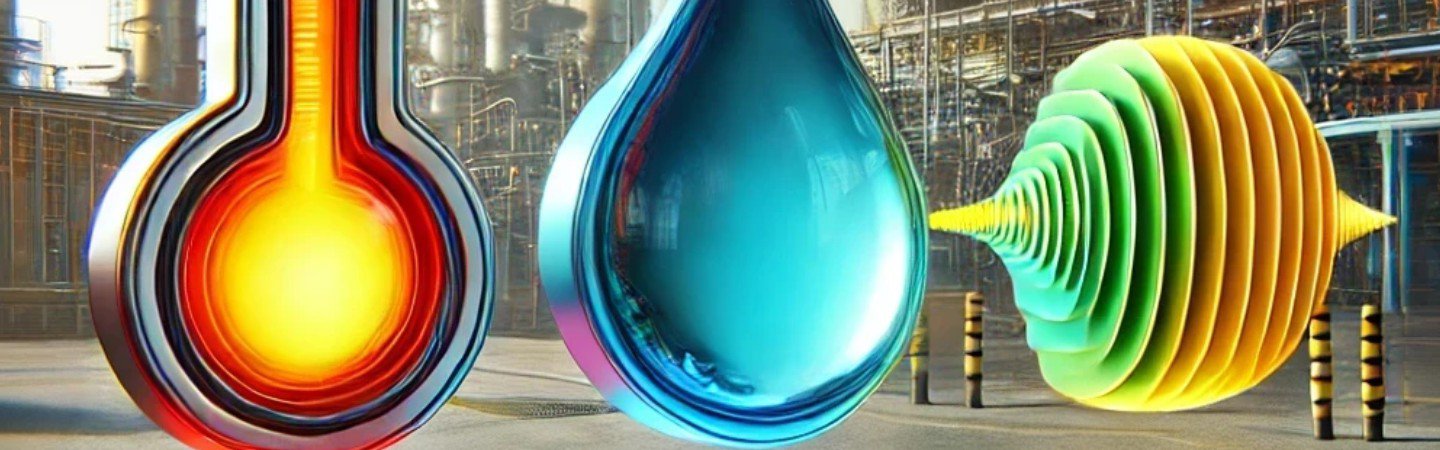
Dan Freeland
09.03.2024
How Smart Sensors are Changing Lubrication in Critical Industries
In the demanding environments of the pulp and paper, wastewater, and refinery industries, maintaining optimal machinery health is critical. Downtime not only leads to substantial financial losses but also poses significant safety and environmental risks. Traditionally, machinery maintenance has relied on routine inspections and reactive repairs. However, we have seen the rise of smart sensors is changing how lubrication is monitored and managed, particularly through the integration of temperature, vibration, and humidity data.
The Critical Trio: Temperature, Vibration, and Humidity in Lubrication
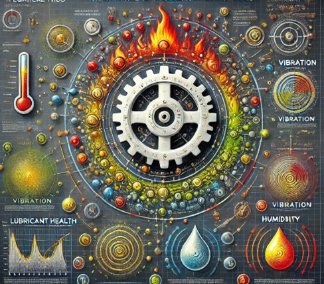
Temperature affects lubricant viscosity, oxidation, and overall stability. High temperatures, commonly found in refineries, can lead to accelerated lubricant degradation, resulting in inadequate protection and increased wear.
Vibration, caused by factors such as misalignment, imbalance, or bearing wear, can induce mechanical stress that accelerates lubricant breakdown. This is particularly challenging in industries like pulp and paper, where rotating equipment operates continuously under heavy loads.
Humidity introduces the risk of moisture contamination, which is especially problematic in environments like wastewater treatment plants. Moisture in lubricants can lead to corrosion, emulsification, and reduced lubrication efficiency, ultimately resulting in increased wear and potential failure.
When these factors are not adequately monitored, they can interact in ways that significantly shorten the lifespan of both the lubricant and the machinery it’s designed to protect.
The Smart Sensor: Real-Time Monitoring and Predictive Maintenance
Smart sensors have introduced an innovative approach to monitoring temperature, vibration, and humidity, providing valuable insights that support predictive maintenance strategies.
Real-Time Temperature Monitoring
In high-temperature environments like refineries, smart sensors continuously monitor temperature to detect subtle changes that could indicate lubricant breakdown or increased friction. By providing trending and near real-time data, these sensors allow maintenance teams to address potential issues before they escalate into failures. For instance, in paper mills, where machinery often operates at high speeds, smart temperature sensors can identify hot spots that signal the onset of thermal degradation in lubricants.
Vibration Analysis for Early Fault Detection
Vibration sensors, equipped with advanced analytics, can identify abnormal patterns that suggest mechanical issues such as misaligned shafts or bearing wear. This is critical in wastewater treatment plants, where pumps and motors are subject to significant vibrational stresses. In refinery operations, detecting unusual vibration patterns early (by comparing them against historical data) can prevent catastrophic equipment failures, ensuring continuous operation and minimizing safety risks.
Humidity Control and Moisture Detection
Humidity sensors play a vital role in environments prone to moisture, such as wastewater treatment facilities and certain areas of pulp and paper mills. By monitoring humidity levels in near real-time, these sensors can detect when moisture begins to contaminate lubricants, allowing for timely intervention. In refineries, where even minor moisture ingress can lead to significant corrosion and lubricant emulsification, humidity monitoring is crucial for maintaining lubricant integrity and preventing premature machinery wear.
The Synergistic Impact of Combined Data
The real power of smart sensors lies in their ability to integrate temperature, vibration, and humidity data into a comprehensive view of machinery health. For example, an increase in temperature, combined with elevated vibration and humidity levels, could indicate that a lubricant is not only breaking down due to heat but is also being compromised by moisture contamination and mechanical stress. In pulp and paper manufacturing, where machinery is subject to both fluctuating humidity and high vibration, the combination of these data points allows for a more accurate diagnosis of potential issues. If a machine exhibits high vibration while temperatures rise and humidity levels spike, it may indicate that the lubricant is failing due to a combination of thermal degradation, moisture ingress, and mechanical wear.
The Power of Trending Data: Unlocking Deeper Insights Over Time
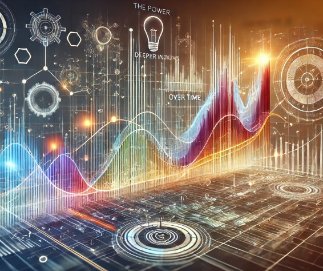
Identifying Long-Term Trends
Trending data allows for the identification of gradual changes in machinery behavior that might not be evident in real-time snapshots. For example, a slow, consistent increase in operating temperature over weeks or months could indicate a gradual decline in lubricant quality, suggesting that an oil change or additional maintenance is required. In the wastewater industry, where machinery operates in harsh environments, trending data can reveal the cumulative impact of humidity and vibration on lubrication, allowing for more precise maintenance scheduling.
Predicting Future Failures
By analyzing trends in temperature, vibration, and humidity data, predictive algorithms can forecast potential equipment failures before they happen. This allows for proactive maintenance interventions, reducing the risk of unexpected downtime and extending the lifespan of machinery. In refineries, where the cost of unplanned downtime is extremely high, the ability to predict and prevent failures based on historical data trends is invaluable.
Optimizing Maintenance Schedules
Trending data helps optimize maintenance schedules by providing insights into how machinery and lubricants behave over time. Instead of relying on fixed maintenance intervals, maintenance can be scheduled based on the actual condition of the equipment, reducing unnecessary interventions and associated costs. In pulp and paper mills, where machinery operates around the clock, this approach ensures that maintenance is performed only when necessary, minimizing disruption to production.
Transforming Maintenance Practices: From Reactive to Predictive
The integration of smart sensors into lubrication systems is driving a shift from reactive to predictive maintenance across these critical industries. Predictive Maintenance: Instead of waiting for failures to occur, companies can now predict potential issues and address them before they lead to downtime. This proactive approach reduces maintenance costs and extends the life of both lubricants and machinery.
Enhanced Safety and Efficiency: In refineries, where the consequences of equipment failure can be severe, smart sensors contribute to safer operations by preventing unexpected breakdowns. Similarly, in wastewater plants, maintaining optimal lubrication through real-time monitoring and trending data analysis prevents failures that could disrupt operations and lead to environmental hazards.
Cost Savings: By extending lubricant life and reducing the frequency of unplanned shutdowns, smart sensors offer significant cost savings. In the pulp and paper industry, where efficient operations are critical to profitability, the ability to monitor and maintain machinery at peak performance provides a competitive advantage.
As the pulp and paper, wastewater, and refinery industries continue to embrace smart sensor technology, the transformation in lubrication monitoring and maintenance becomes increasingly apparent. The integration of temperature, vibration, and humidity data, combined with the power of trending analysis, offers a deeper, more nuanced understanding of machinery health. This enables more precise and proactive maintenance strategies, enhancing reliability, safety, and efficiency.
The future of lubrication management is not just smart—it’s data-driven. The industries that adopt this technology will lead the way in operational excellence, sustainability, and innovation.