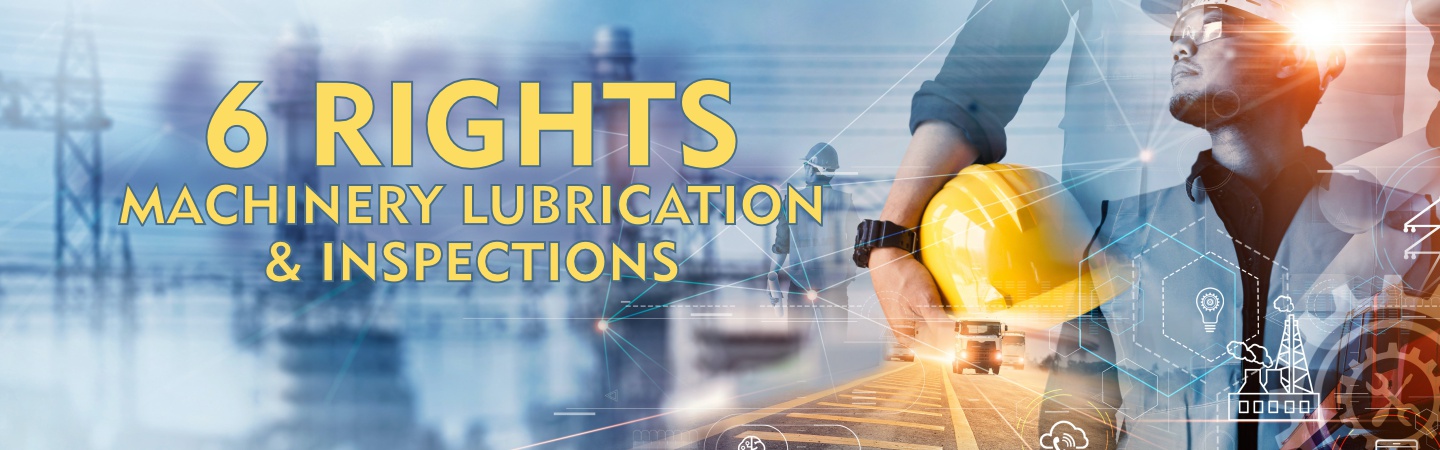
Dan Freeland
08.06.2024
Equipment Condition-Based Monitoring vs. Time-Based Equipment Inspections
In machinery lubrication, what has been known as the 5Rs has been around for probably 20 years or so. They are acknowledged as fundamental principles for lubrication and have been written about many times in books, articles, blogs, etc These 5Rs are the backbone structures for writing proper lubrication procedures and developing a successful lubrication program. We at Trico also like to include a sixth “R”. That refers to the “right personnel”. This means the proper personnel are certified and trained in how to properly perform lubrication related tasks. In recent internal discussions, we were talking about how these 5R’s can be related to machine inspections. Not only that, but how does the emergence of condition-monitoring technology work within the parameters of those 5R’s and how do they relate to machine inspections?
The Right Lubricant
I guess we’d have to ask the question, what happens when the wrong lubricant is either topped off or completely replaces the correct lubricant? Well, lubricants are selected based on factors like temperature, load, and speed. If the wrong lubricant is used, it can lead to chemistry issues with the lubricant and increased wear, which both result in higher temperatures over time. Will a machine inspection catch incrementally rising temperature changes? Probably not. Not if the traditional way of putting your hand on it is used. How long will it take to identify this in a typical machine inspection cycle for that machine? I guess you’d have to wait and see, and once it does reach a critical temperature, when is the next machine inspection to identify it? By then, is it too little too late?
Condition Monitoring Influence:
Monitoring: Machine Vitals can monitor oil properties like temperature trends to detect if the lubricant in-use might be degrading or if the wrong type of oil has been applied.Alerts: If the system detects abnormal lubricant behavior, it can alert maintenance personnel to verify the lubricant type and quality, helping catch issues early even if inspections are missed.
The Right Quantity
Having too much or too little lubricant in the machine? Our testing has shown, and it stands to reason, that both conditions cause temperature increases in the lubricant. If the oil is too high, the components work harder to get through the lubricant. It also causes foaming, frothing, and potentially lubricant leaking out of the shaft seals. If the lubricant is too low, obvious metal-to-metal contact between the components is sure to come. This causes higher temperatures in the component area, component failure, and will lead to failure. Now, is a machine inspection going to catch this? Probably. Checking the lubricant level is probably the most basic action to check off in an inspection. But is the inspection being done properly, has it been “rubber stamped”, or is it just that no one has had the time to get out there and do it? It sounds like an unnecessary risk that can be avoided.
Condition Monitoring Influence:
Anomaly Detection: If the monitoring system detects that lubrication levels are consistently too high or too low, it can trigger an alert, prompting immediate manual inspection or corrective action.
The Right Location
Lubricants must be applied to the correct points on a machine to be effective, especially in complex equipment with multiple lubrication points. Inspections should verify that lubricants are reaching the intended components, such as bearings, gears, or seals. This might include checking for blocked or damaged lubrication lines and ensuring that all critical components receive adequate lubrication. If any of these points are overlooked, how will anyone know?
Condition Monitoring Influence:
Vibration and Temperature Monitoring: Machine Vitals can use IMU (Inertial Measurement Unit) sensors to detect increased vibration levels or temperature spikes in specific components, which might indicate that lubrication is not reaching critical areas. Predictive Analytics: The system can analyze trends in data to predict when and where lubrication failures might occur, allowing for proactive maintenance even if routine inspections are overlooked.
The Right Time
This R is probably the most prominent when it comes down to condition-based monitoring compared to equipment inspections. Finally, when is the right time to do an inspection? These are usually done on a time basis, not a condition basis, so what happens when the inspection is done and something changes right after it? I guess you wait until the next time someone gets to it. Is that again too little too late?
Condition Monitoring Influence:
Monitoring: Machine Vitals is always watching. Any time humidity, temperature, pressure, or vibration monitoring rises above predetermined thresholds. That is when machine inspections need to take place, not simply relying on a time-based inspections. This saves valuable time by doing inspections when and where they need to happen, and not worrying about the reliable machines that are reporting standard operating parameter ranges. Event Logs: Maintenance events can be recorded to provide background on anything done to the equipment. This is invaluable information to determine why a parameter or parameters are running outside of normal operation and assist in the actual machine inspection when needed.
The Right Method
The method of application—manual, automatic, or centralized lubrication systems—should be appropriate for the machinery and operating conditions. Inspections should verify that the correct application methods are used and that any automated systems are functioning properly. Inspectors should also ensure that the correct tools and procedures are being followed, such as avoiding contamination during lubrication. Human error is one of the leading causes of lubricant contamination in a machine. Equipment inspections don’t typically allow the personnel to “see” contamination entering a piece of equipment. Particulate and water contamination are the leading causes of component failure. However, particulate contamination is rarely seen in an inspection and in the case of water contamination, being able to physically see water in the form of an emulsion or free water is often too late.
Condition Monitoring Influence:
System Health Checks: Machine Vitals can monitor the health and performance of automated lubrication systems, ensuring they are working correctly. If a system is not applying lubricant as expected, the sensors can detect this and notify maintenance teams. Humidity can also detect the presence of water, alerting the need to address it before a damaging situation occurs. Method Verification: By analyzing the consistency and effectiveness of the lubrication application by monitoring temperature, pressure, and even vibration, the system can confirm that the correct methods are being used, even in the absence of manual verification.
The Right Personnel
We are all struggling with the personnel issues that face our industries. First of which is not enough people. Budgets are tighter than ever, and managers are constantly forced to do more with less. Lubrication-related preventative measures are typically the first to be stricken from the daily “to-do” list. Secondly, finding qualified people. The baby boomers are retiring and taking all their years of tribal knowledge with them. That sort of real-life experience and education is not easily replaced. Third, managers are stuck relying on in some cases, unqualified and even untrusted individuals to perform these equipment inspections. There is no way of knowing if the inspections are being done properly or if at all. All of these can lead to potentially catastrophic lubrication issues.
Condition Monitoring Influence:
Training Gaps Identification: If Machine Vitals detects recurring issues related to improper lubrication, it can highlight potential training gaps in the maintenance team, prompting a review of procedures and training. Automated Reporting: Augmented with a quality oil analysis program, condition monitoring can generate detailed reports relating to lubrication performance, providing insights into whether maintenance practices align with best practices, thus ensuring accountability and improving personnel performance.
Condition-Based Monitoring (Machine Vitals) acts as a safety net, ensuring that critical lubrication tasks are not overlooked, even if human inspections are not performed as expected. By continuously monitoring machine health through sensors and advanced analytics, it provides real-time insights and alerts that help prevent lubrication-related failures, supporting the overall reliability and efficiency of industrial equipment. This ensures that the "6 R's of lubrication" are adhered to, reducing the risk of equipment failure and extending machinery life.