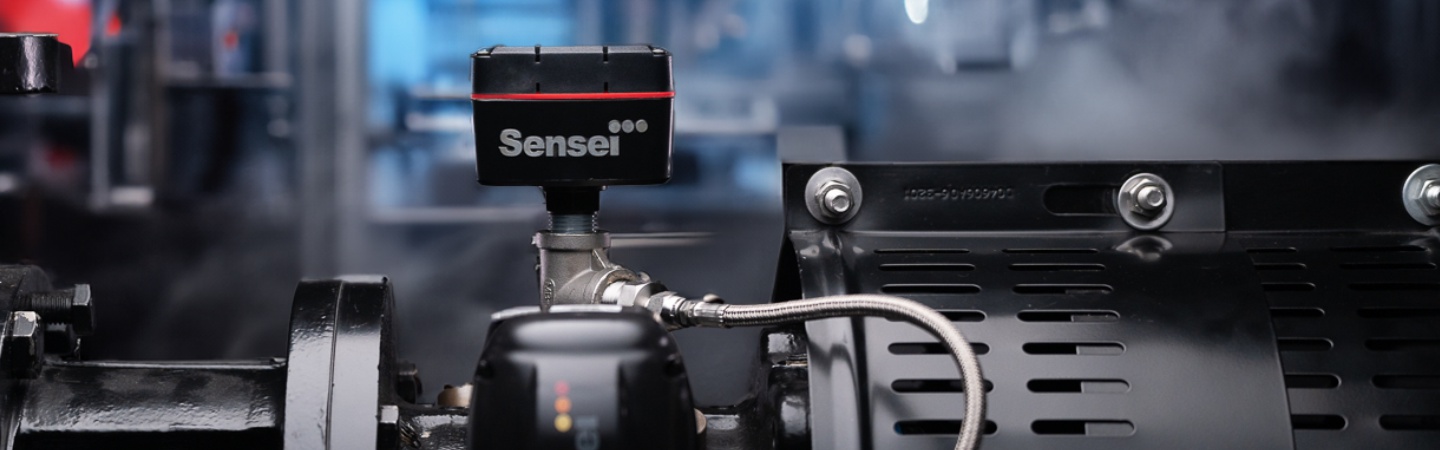
Dan Freeland
10.01.2024
Predictive Insights for a Reliable Equipment
When it comes to industrial maintenance, avoiding unexpected equipment failures is crucial. Picture your machinery as a marathon runner: if it breaks down mid-race, you're not just losing time—you’re losing money. This is where condition monitoring comes into play, providing a proactive approach to equipment health. By using advanced condition monitoring devices, maintenance supervisors can significantly reduce costly downtime and maintenance expenses. With technologies like Machine Vitals, industries can prevent breakdowns before they occur, ensuring smooth and efficient operations—and keeping your machinery running the marathon without spraining an axle.
What is Condition Monitoring?
Condition monitoring is like having a doctor who can spot trouble before you even feel a twinge. It's a proactive maintenance strategy that involves continuously checking critical parameters to assess the health of machinery. This isn't your typical yearly check-up—it's more like your equipment has a personal trainer watching its every move, or like your fitness tracker for rotating equipment. Technologies such as vibration monitoring devices and temperature sensors are the stethoscopes and thermometers in this scenario, providing essential insights into equipment conditions. Whether it's a bearing condition monitoring device or a motor condition monitoring device, these tools help maintenance teams predict and prevent failures, ensuring your machines don’t just live long but prosper.
Early Detection of Wear and Tear
Think of continuous condition monitoring as the “early bird” that catches the proverbial worm—or, in this case, the minor issues before they turn into full-blown disasters. It’s like spotting a tiny pebble in your shoe before it gives you a blister. Vibration monitoring is crucial for identifying mechanical imbalances in rotating devices, while other condition monitoring parameters for pumps and gearboxes, in particular, play a vital role in industries where even a small hiccup can halt operations and lead to significant financial losses—because nobody wants to be the one explaining why a million-dollar production line is down due to a $5 bearing failure.
Key Parameters Monitored by Machine Vitals
Temperature - Imagine your equipment is having a fever, and you’re blissfully unaware until it’s too late. Overheating can lead to catastrophic failures, especially in rotating equipment. Machine Vitals monitors both internal and external temperatures, helping to identify conditions such as excessive friction or cooling system failures. It’s like having a thermometer that not only takes the temperature but also alarms, “Hey, your gearbox is running a bit hot today—maybe check on it”. By dealing with these issues early, Machine Vitals helps prevent overheating, reducing the risk of damage and unplanned downtime. This makes temperature monitoring sensors indispensable for maintaining the reliability of rotating equipment. Vibration - Vibration monitoring is another cornerstone of effective condition monitoring. If your equipment starts to shake, rattle, and roll—outside of a rock concert—you’ve got a problem. Excessive or unusual vibrations can indicate a range of issues, from unbalanced components to misaligned shafts or deteriorating bearings. Machine Vitals uses advanced vibration monitoring devices to track these patterns in near real-time. By analyzing vibration data, the system can alert operators to potential mechanical problems long before they result in equipment failure. This type of rotating machinery vibration monitoring is essential for keeping your machinery humming smoothly—no literal head-banging is required.
Acoustic Data - If you’ve ever cringed at the sound of your car making a weird noise, you already understand the value of acoustic monitoring. Machine Vitals uses acoustic sensors to capture and analyze sound data, identifying irregularities that may indicate bearing wear or other hidden problems. It’s like having a stethoscope for your equipment, picking up on every whistle and murmur. As a monitoring device, Machine Vitals can catch early signs of failure that might be missed by other methods, allowing for timely interventions and preventing costly repairs or replacements.
Humidity - Humidity might be good for your skin, but it’s terrible for your machinery. Excessive moisture can lead to corrosion and contamination of lubricants, accelerating wear and tear. Machine Vitals monitors humidity levels both inside and outside the equipment, ensuring that environmental factors do not compromise machinery health. This humidity condition monitoring capability is particularly valuable in gearboxes, pumps, and hydraulic tanks, where even a little bit of moisture can lead to a whole lot of trouble. Think of it as your equipment’s smart dehumidifier, keeping things dry and happy.
Pressure - Pressure monitoring is the unsung hero of the condition monitoring world. If your machinery’s internal pressure is out of whack, it’s like trying to breathe through a straw. A sudden change in internal pressure can indicate a blocked desiccant breather or compromised shaft seal, both of which are crucial for protecting the internal environment of machinery. Machine Vitals tracks pressure differentials within the headspace and ambient environment, allowing early detection of these issues. It’s like having a virtual expert who nudges you and says, “Hey, something’s not quite right here—check the seals!” By addressing pressure imbalances promptly, Machine Vitals helps prevent contamination, ensuring the longevity of lubricants and the overall health of the machinery.
Machine Vitals Extending Equipment Life
Preventing Gearbox Failures - Gearboxes are the silent workhorses of many industrial settings, and when they fail, the silence is deafening. Machine Vitals continuously monitors key parameters such as temperature, vibration, pressure, and humidity within gearboxes. By detecting issues like lubrication degradation, pressure anomalies, or the presence of contaminants, Machine Vitals helps prevent catastrophic gearbox failures. This proactive gearbox condition monitoring enables timely maintenance, avoiding unexpected shutdowns and extending the lifespan of these vital components—because nobody wants to explain why the entire line is down due to a busted gearbox. Enhancing Pump Reliability - Pumps are the heart of many industrial processes, and their reliability is often overlooked. Machine Vitals offers comprehensive monitoring of industrial pumps, focusing on bearing conditions, vibration levels, pressure, and internal humidity. By catching early signs of bearing wear, lubrication failure, or pressure anomalies indicating seal issues, Machine Vitals can alert maintenance teams before a pump failure occurs. This level of condition monitoring for rotating equipment ensures that pumps operate reliably, reducing maintenance costs and enhancing overall system performance—so your operations don’t come to a screeching halt because of a bad pump.
Hydraulic Reservoir Health Monitoring - Hydraulic systems are like the nervous system of industrial equipment, transmitting power and control throughout the machinery. The health of hydraulic reservoirs is crucial, as they store and condition the hydraulic fluid that keeps everything running smoothly. Machine Vitals monitors key parameters such as temperature, humidity, and pressure within the reservoir, detecting early signs of fluid degradation or contamination. By keeping an eye on pressure changes, Machine Vitals can identify issues like blocked desiccant breathers or compromised seals, which can lead to moisture ingress and fluid oxidation. Catching these problems early prevents costly hydraulic failures and extends the life of both the reservoir and the entire hydraulic system -because no one wants their machinery paralyzed by a hydraulic fluid crisis.