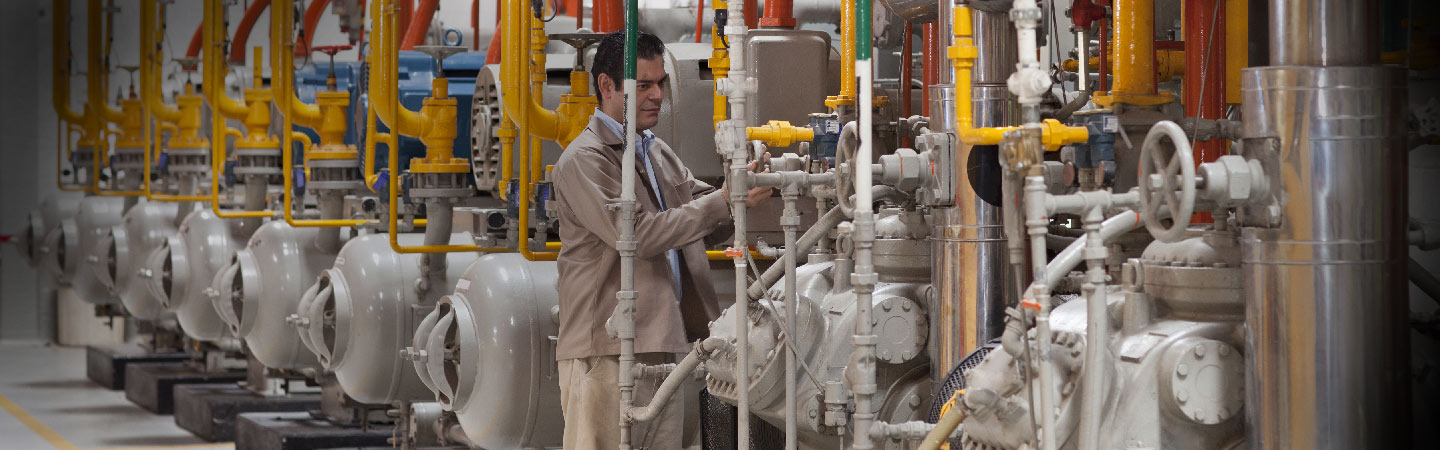
Justin Kolterman
09.17.2019
Why It’s Important to Frequently Collect and Analyze Data About Your Oil’s Physical Condition
Do your techs do lube routes? Stopping at critical equipment around your facility on a regular interval remains a vital practice for maintenance and reliability.
But if your techs look at the job as only about making sure all the right points have a sufficient amount of lubricant, then you’re missing a great opportunity. While they’re there, they can collect and analyze a key piece of oil intelligence – observation of the physical condition of the oil.
Inspection at the machine is the right time to check not only oil level, but also things like temperature, sight and smell. Is the lubricant dark, discolored or foamy? These notes may be your first indication that something’s amiss.
Here are just a few examples of physical condition observations and what they may mean.
Look.
Visual inspections of equipment may yield insights such as:
- Mist in the air, which could indicate volatiles coming off a machine, which would ultimately increase the drag, friction and heat in your equipment.
- Slime on filters and equipment, which could indicate a fungal or bacterial problem.
- New oil that looks light yellow or dark amber, which could indicate extreme oxidation or the wrong lubricant.
Listen.
Knocks, pings and other unusual noises may mean insufficient lubrication.
- Lubricant may not be getting to where it belongs.
- The machine may be straining harder than usual or recommended.
Smell.
Several distinct odors indicate the presence of a problem.
- A sulfur, or rotten egg, smell could indicate a bacteria problem.
- A wet, dirty odor (similar to nasty gym socks) could indicate a fungal problem, which can happen to oil as well as water.
- Solvents, ammonia and gasses such as nitric oxide or argon could indicate leaks or other safety issues.
What to Do with Your Observations
It takes some experience to be aware of these different situations, let alone diagnose what they mean. These days many facilities lack the right expertise, so perhaps the most important thing to do if you and your team see, hear or smell something that might be wrong is to take samples and get expert oil analysis input.
When considered through the lens of experience along with these insights about physical conditions as well as info about the machine/application and lubricant’s journey throughout your facility, oil analysis is transformed into powerful Oil Intelligence you can act on to prevent, predict and optimize.
Did you know? You don’t necessarily need to send your techs out to the machine in order to keep an eye on the oil level? Sensors can do it for you.
- Category:
- Application
- Tags:
- Physical Condition
- Lifecycle