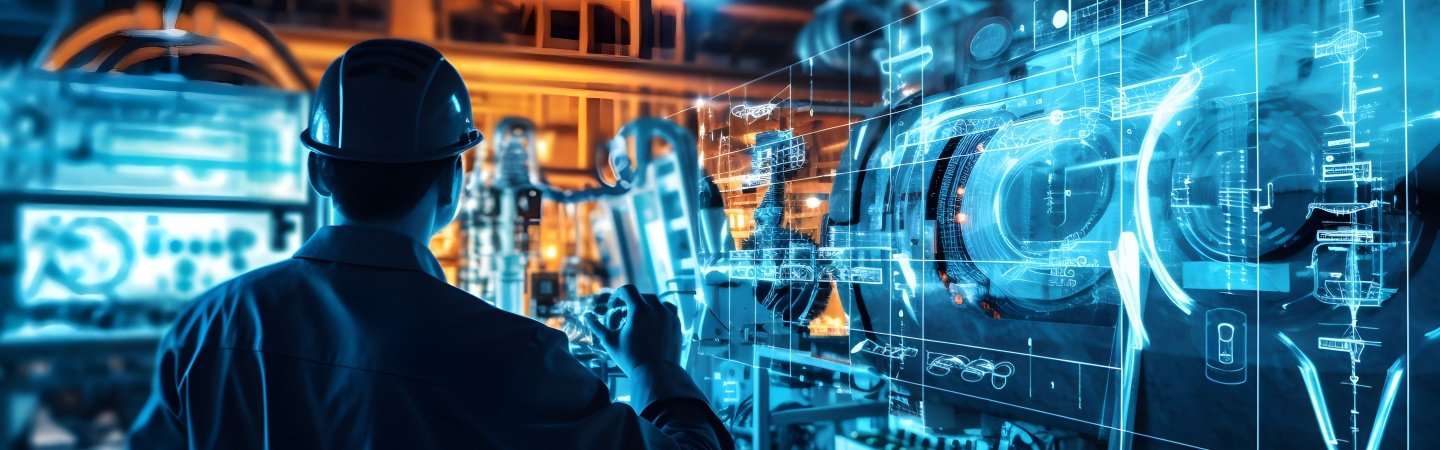
Dan Freeland
09.12.2023
Maximizing Efficiency and Preventing Downtime through Proactive Maintenance Strategies
As a maintenance manager or reliability professional, you know how important it is to keep your equipment running smoothly. Downtime can quickly lead to lost productivity and revenue, which is why it's crucial to stay on top of proactive maintenance strategies. One of the most effective ways to achieve this is through condition monitoring, the process of monitoring the health of your equipment to detect problems before they become serious. In this practical guide, we'll explore the various types of condition monitoring techniques available to help you unlock maximum efficiency and keep your equipment in top shape.
Understanding the Basics of Condition Monitoring
Condition monitoring involves regularly checking equipment for signs of wear, damage, or other issues that could lead to breakdowns or malfunctions. The goal is to catch problems early on, before they cause major disruptions to operations. There are several different types of condition monitoring techniques, including vibration analysis, oil analysis, infrared thermography, and ultrasonic testing. Each method focuses on measuring specific parameters and analyzing data to identify potential issues. Oil analysis, however, is the only type that truly examines the lifeblood of your equipment.
The Benefits of Condition Monitoring
One of the primary benefits of condition monitoring is increased equipment efficiency. By catching problems early on, you can address them before they escalate and cause major damage. This not only reduces downtime but also prolongs the life of your equipment, saving you money on costly repairs and replacements. Additionally, condition monitoring helps you make more informed decisions about maintenance schedules, as you'll have a clearer picture of when maintenance is actually needed.
Choosing the Right Condition Monitoring Technique
Every piece of equipment has unique needs, and the same goes for condition monitoring techniques. The key is to choose the right method for each specific piece of equipment, taking into account factors like cost, complexity, and accuracy. For example, vibration analysis is often used for rotating equipment like pumps and motors, while oil analysis is more commonly used for hydraulic systems and gearboxes.
Implementing a Successful Condition Monitoring Program
To get the most out of your condition monitoring program, it's important to start with a solid plan. This includes defining your goals, identifying the equipment to be monitored, and selecting the right technique for each component. You'll also need to establish monitoring schedules and procedures, including how to collect and analyze data. Speaking of data, the data means nothing if it is not understood. No matter which technique(s) you choose to implement, be sure to partner with industry professionals who will help you weed through the data and give you informed insights into what your data is telling you. Finally, make sure you have the right tools and software in place to manage your program effectively.
Embracing the Future of Condition Monitoring
As technology continues to develop, so too do the possibilities for condition monitoring. One exciting new trend is the growing use of onboard wireless sensors, which leverage advanced analytics and machine learning to predict when equipment failures are likely to occur. This allows maintenance teams to take proactive steps to prevent breakdowns before they happen, further increasing efficiency and reducing downtime. Stay apprised of the latest sensing technologies for your equipment. These sensors will revolutionize your maintenance strategies and scheduling, all from your laptop or other computing devices.Condition monitoring is a powerful tool for maintenance managers and reliability professionals, allowing you to stay ahead of potential equipment problems and maintain maximum efficiency. By understanding the basics of condition monitoring, choosing the right technique for each piece of equipment, and implementing a well-planned program, you can proactively manage your equipment and avoid downtime. Embracing new technologies like predictive wireless sensors can take your program to the next level, providing even greater insights and efficiencies.