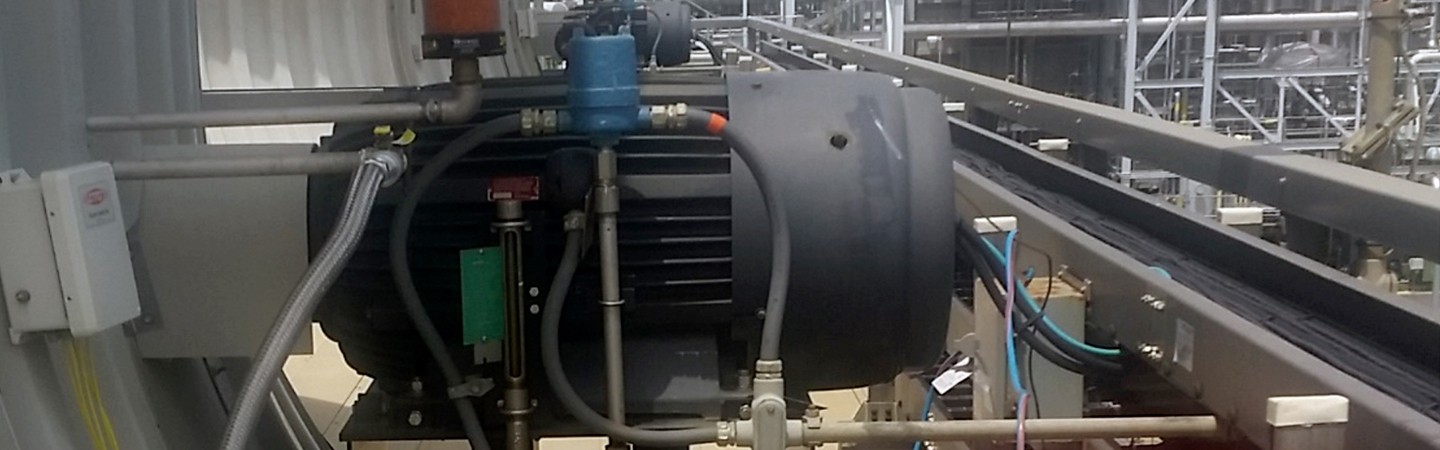.jpg)
Mike Gauthier
10.29.2019
Trico Data Showed 75% of Gearbox Oil Samples Exceeding Contamination Limits
Can we all agree that repairing or replacing an SPX or Amarillo cooling tower gearbox is a pricey pain?
$50K just for the part – not including the labor and downtime costs.
The gearbox is basically inaccessible and out of sight, so is there anything you can do to avoid the headaches of an unplanned outage?
The answer is yes. Let’s break down the cooling tower gearbox issue a bit.
How Likely Is a Gearbox Failure?
Gearbox lubricants need to be clean to help minimize friction, so maintaining the ISO 4406 target cleanliness code of 18/16/13 is critical.
When Trico recently reviewed results from 3,000 gearbox oil samples, we found that as much as 75% of them were over the acceptable cleanliness standards.
Many facilities are putting their gearboxes at risk. You can do better.
When Should You Change the Cooling Tower Gearbox Oil?
Without knowing the condition of gearbox oil at any given time, many plants simply change the lubricant at a set interval. If you’re using a mineral oil, or your facility is in a harsh climate (high heat and humidity), the major gearbox manufacturers recommend changing out the oil as frequently as every 2-3 months.
If you’re using an advanced synthetic ISO 220 lubricant under ideal conditions, they say you can go up to 5 years between oil changes.
But you probably don’t want to push it that far without knowing the condition of the oil.
How Do You Know the Condition of the Gearbox Oil?
Regardless of what kind of lubricant you start with, the only way to know how the oil is doing is through sampling and analysis as close to the live zone as possible, as well as at other points in your process and throughout your facility.
You should test your lubricant at least quarterly, gearbox manufacturers say.
But that’s easier said than done because many cooling towers lack a convenient means of extracting a sample.
How Can You Keep the Oil Clean and Reduce Oil Changes?
Contaminants can get into your machinery oil in lots of different ways – including storage, handling, transfer or even transport to your facility. There isn’t a cure-all for these challenges.
When you’re specifically considering cooling tower gearboxes, here’s the approach we recommend. Use a single, portable lubricant filtration cart, which can serve all your cooling tower gearboxes.
Using a filtration cart:
- Potentially extends oil change interval by filtering out contaminants.
- Extends the life expectancy of the gearbox.
- Provides a good sampling location so you can monitor oil condition.
- Costs less than 10% of a single gearbox repair.
Depending on your oil analysis results, which help determine filtration needs, you might hook up the filtration cart for an hour and a half, once a month. That’s a lot less disruptive than the oil changes or the unplanned downtime that you’d be helping to avoid.
Initial Results from a Power Plant Installation
A power plant operator implemented this filtration cart solution with desiccant breathers on 13 cooling tower gearboxes, and the results so far have been great.
Samples from those gearboxes are averaging ISO 4406 code particle counts of 18/16/12. These numbers are at or below the limits for gearbox lubricant, and they’re two ISO code levels below the average numbers Trico was seeing in those 3,000 gearbox oil samples we aggregated – translating to a reduction in the lubricant particle counts by up to 75%.
Discover the Trico Cooling Tower Gearbox Protection Kit
Download the PDF below to learn more about a filtration and sampling solution that can help you reduce costly oil changes, repairs and downtime.