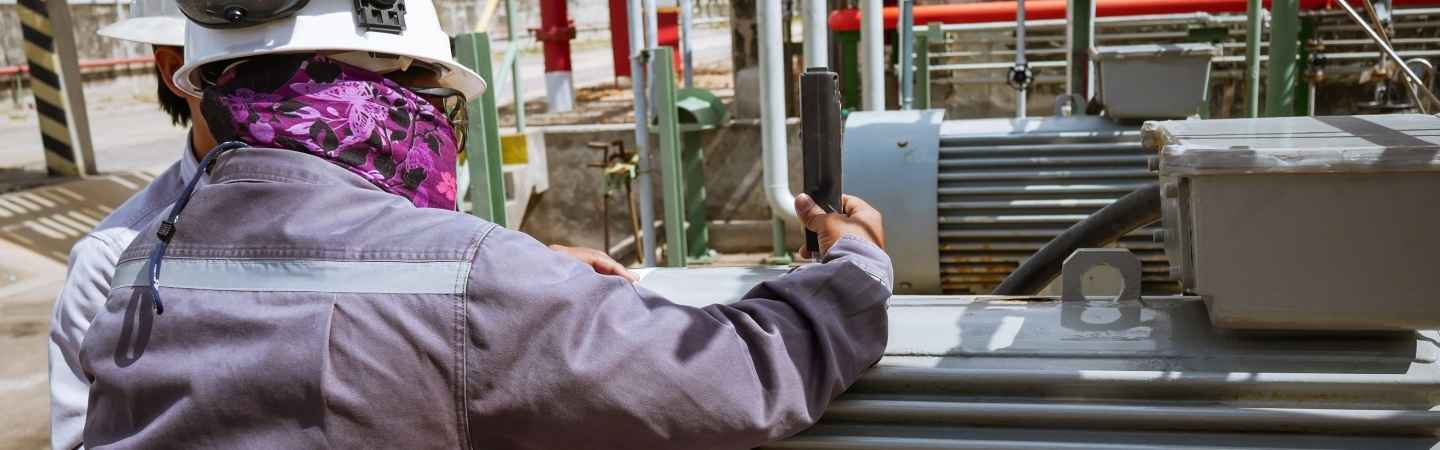
Dan Freeland
12.19.2023
Moving from Reactive to Predictive Maintenance
Unplanned downtimes due to reactive maintenance can cause an enormous strain on production, motioning, and services dependent on machinery. Not only does it affect the revenue stream, but it can also have a lasting impact on company culture, safety, and reputation. Hence, industry leaders have been searching for a solution that can help them replace traditional reactive maintenance with a more proactive and eco-friendly maintenance option. Thanks to the advancement of online sensing, the dream of predictive maintenance is no longer a figure of the imagination but a reality.
The cost associated with unplanned downtimes due to reactive maintenance has always been a significant concern for businesses. The downtime alone can be prohibitively expensive, and the subsequent repairs and emergency services can push the cost even higher. Thanks to predictive maintenance that utilizes online sensing, businesses can now prevent unexpected downtimes. This technology allows for the monitoring of machine performance in real-time and predicts when maintenance is required, reducing the need for unplanned repairs or replacements, minimizing production downtime, and avoiding subsequent safety risks.
However, predictive maintenance may seem complicated and sophisticated, but the process has been made easy with the use of online sensing and web-based software. Online sensors are installed on different equipment, sense variables like temperature, vibration, humidity, and more. Data from these sensors roll up on cloud-based analytics software that analyses the machine data to understand the equipment usage patterns and alert maintenance personnel if any potential anomalies are detected. By following these patterns, these sensors predict the future requirement for maintenance, allowing maintenance personnel to focus on the machines that require attention, and reduce the discrepancies and cost associated with upkeep.
Another key advantage of predictive maintenance is that it also extends the life of the machinery. In contrast, businesses save money by minimizing the need for replacements and repairs by tracking usage and detecting failure patterns, thereby prolonging the lifespan of equipment. This ultimately reduces the environment's carbon footprint, and an added advantage is the positive impact on the company's public image.
With online sensing technology in its early stages, predictions suggest the industrial sensor market will reach over 50-billion-dollar investments in the next decade. This technology could potentially revolutionize traditional maintenance practices and enhance the standard of life for people worldwide. Furthermore, the integration of predictive maintenance with the Internet of Things (IoT) can transform many industries by enhancing efficiency and reducing risk. When combined with connectivity and machine learning, maintenance teams can diagnose faults, track, and fine-tune solutions preceding failures. By spotting possible issues before they occur, supported by reliable data, maintenance teams can take corrective actions that are much more efficient, effective, and less disruptive in terms of the bottom line.
Online sensing and web-based software are revolutionizing the maintenance sector by taking a proactive approach to maintaining crucial machinery. With predictive maintenance, the costs associated with unplanned downtimes are reduced, and machine lifespan is prolonged, which has a lasting positive impact on the environment. The use of online sensors and predictive maintenance is a practical investment for industries, as it is cost-effective in the long run, reduces unplanned downtimes, improving safety and maintaining machinery lifespan. As we move towards a more sustainable future, this technology could transform traditional maintenance practices and prove to be a game-changer for businesses.
- Category:
- Lubrication Program
Recent Posts
-
Is Your Equipment’s Health Checkup Stuck in the Past?
-
The Pulp and Paper Industry in the Digital Era
-
The Fitness Tracker for Your Industrial Equipment
-
The Year of Lubrication Management
-
Oil Analysis in 8 Steps
-
Enhancing Industrial Safety
-
Lube Routes
-
How Machine Vitals Reduces the Impact of Labor Shortages on Maintenance