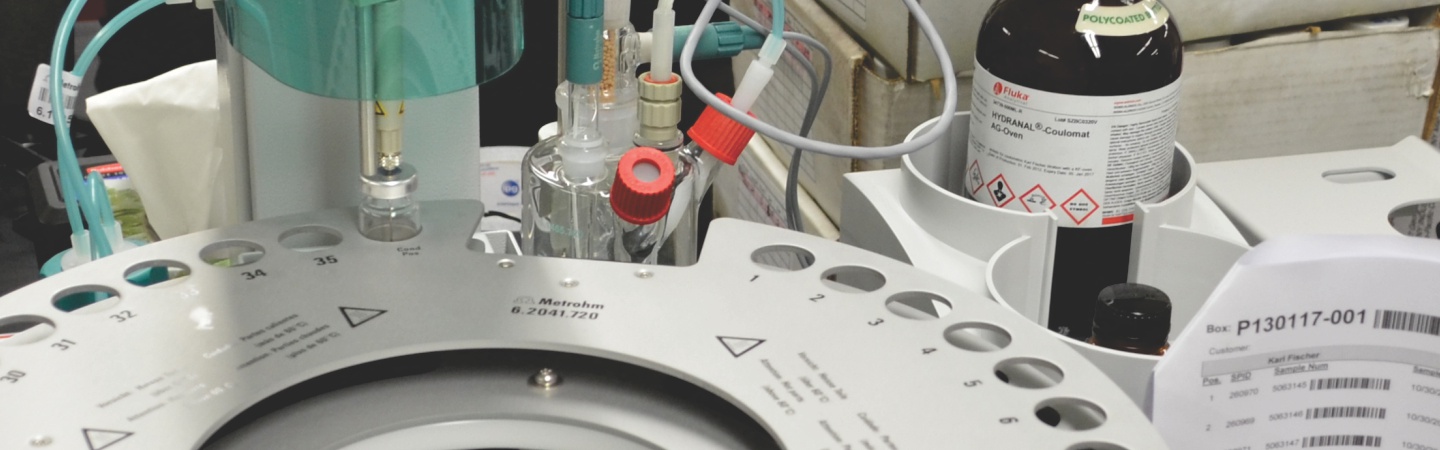.jpg)
Victoria Bunchek
03.22.2022
Why Karl Fischer is on the “A List”
Water can damage components because it does not react like oil under pressure. When lubricant is squeezed by the operating loads and speeds at a single point of contact the pressure can be immense. While these pressures cause oil to momentarily solidify, water will instantaneously boil which produces a super-pressurized bubble between the metal surfaces. If/when this bubble pops (more like explodes) it can cause tiny surface cracks that erode the metal and causes damage called “cavitation” or “water erosion/etching”.Equipment is not the only thing susceptible to water damage. Water can be detrimental to lubricating oils as well. The presence of water can alter the viscosity of the lubricant as well as cause chemical changes resulting in additive depletion by washout and the formation of sludge, varnish, and acids. Below is a list of other issues due to water contamination:
- Hydrolysis, or destruction of the lubricant
- Red oxide formation (rust)
- Hydrogen embrittlement
- Corrosion due to acid production
- Loss of lubricant film
Tests for Water
There are several different methods for water detection, but they all come with advantages and disadvantages. Crackle Test
The Crackle Test is a simple method in determining the presence of water in a lubricant. With this method the lubricant is placed on a hot surface which causes any presence of water to crackle and sputter as it boils off. This test is qualitative, it only determines the presence of water, it does not put a value to the amount of water present. Typically, this test is performed first to determine if water is present before performing additional water tests that are little more costly. The downside to this test is that each lubricant reacts to water differently – either absorbing or shedding it and this will influence the concentration of water that causes a positive crackle. The lubricant will also react differently based on its age and cleanliness.
Fourier-Transform Infrared Spectroscopy (FTIR)
Fourier-Transform Infrared Spectroscopy is often used for identifying chemicals based on the wavelengths of light that are absorbed by the substance molecules. These quantities can indicate the existence of severity of chemical degradation that can take place in the lubricant once the water has started to react with the base oil or additives. While an important test, this is most useful to determine if the detrimental effects of water contamination are present. Since different molecules will share similar characteristics, this type of testing can easily misrepresent the amount of water present in a sample.
Karl Fischer (KF)
Karl Fischer is specifically designed to quantify the amount of water in a lubricant. The process involves a chemical reaction between water in the lubricant and iodine. An electrical impulse is created when the water reacts with iodine. The intensity and duration of the electrical impulse is measured and converted to a concentration of water. The value for this test is more useful since it is reported as a concentration of water in the lubricant (parts per million, ppm, and percent).
Karl Fischer testing is the most widely accepted method for detecting water in lubricating oils due to its extreme accuracy and reproducibility. It can detect both high levels and trace water content in free, dissolved, or emulsified form.
The “A List”
As you can see there are many reasons to test for water content in lubricating oils, but it is sometimes difficult to decide on which test method to use. Although the crackle test is easy to use it lacks precision and accuracy. If only a general idea of whether water is present is needed, then FTIR is best used. However, this method is prone to interferences and cannot detect extremely low levels of moisture. If accuracy, precision, and repeatability are required, then the Karl Fischer method should be on your “A List”.
Create a Plan of Action
We can help you create a plan of action to monitor and prevent water contamination. Click below to receive help from a lubricant consultant at Trico.
- Category:
- Oil Analysis
- Contamination
- Tags:
- Water Contamination