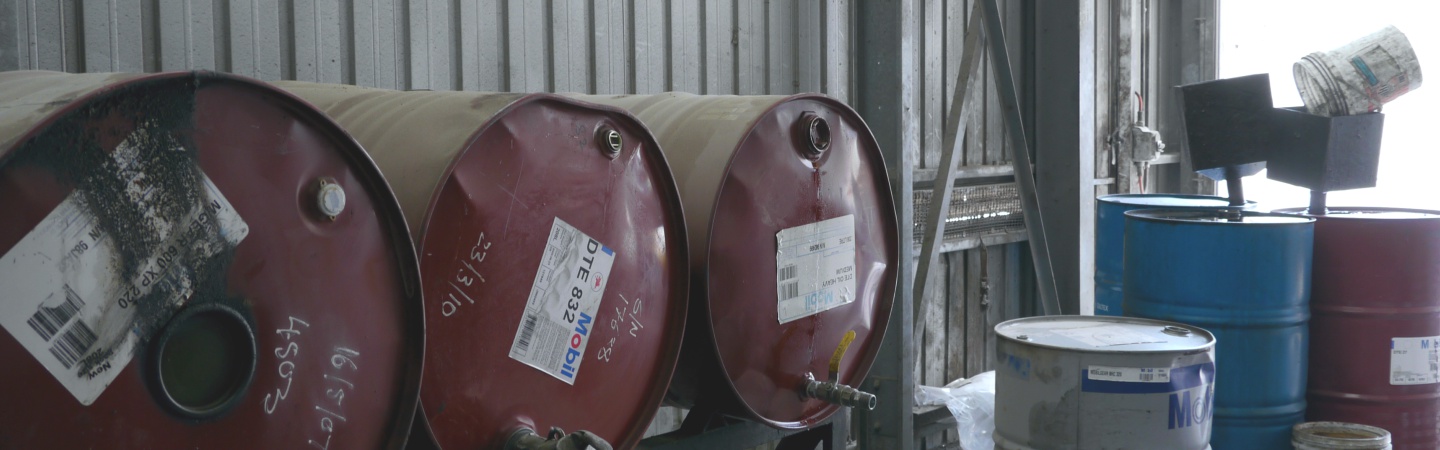
Mike Gauthier
08.18.2020
Protecting your Lubricant Throughout Its Journey
Maybe it’s just a few specks of dust. Or a couple droplets of moisture.
These sneaky undesirables can get into your lubricants and quickly compromise your assets.
Costly, unplanned machine downtime may follow.
That’s why it pays to be vigilant against contaminants throughout the entire journey of the lubricant. Because contamination threats are lurking at every stage.
To reduce contamination threats, here’s what to watch out for.
Arrival and Storage
- Untested Shipments – When lubricant arrives at your facility, it’s not as clean as you may think because contamination can occur during vendor storage, handling, packaging, and transporting.
- Inadequate Space – The lack of a dedicated area for lubricant could cause contamination ingression and compromise its quality.
- Open Oil Drums – A basic mistake can have devastating impact on the overall effectiveness of your lubrication program.
Transferring
- Dirty Containers – Transferring lubricant using containers and/or funnels that have not been properly cleaned can lead to the introduction of contaminants or cross-contamination.
- Cluttered Storage Area and Shelves – Not only do disorganized and dirty storage areas lead to particulate contamination – it’s also easy for the wrong lubricant to get used.
- Poor or No Filtration – Filtering new oil prior to it being put in use ensures you are putting cool, clean and dry oil into your most critical assets. It’s also very economical costing 1/10 less than the oil in use.
Application
- Unnecessary Maintenance – Even basic tasks can introduce contaminants into the lubricant and equipment. Target equipment that needs attention.
- Equipment Strain – Changes in production cycles and seasonal conditions can affect equipment and lubricant in significant ways.
- Unchecked Ancillary Sources – System vents, coolers, heat exchangers, or exposure to outside can cause water and particulate contamination.
People and Processes
- Inadequate Tagging – Not having a tagging system to properly identify the lubricants can cause cross-contamination and misapplication.
- Rushed Technicians – An oil sample gathered from the wrong location or improperly extracted because the technician is pressed for time does not yield accurate results and may disguise an issue.
- Incomplete Training – Without clear guidance on best practices, employees can introduce all kinds of issues.
- Unsupportive Management – Employees need management support and achievable goals for measured results, or they won’t know what’s working and what to improve.
- Unnecessary Oil Changes – changing oil based on time and not condition can lead to introducing contaminants through process and human error.
Awareness is Key
You can protect your lubricant and equipment by being aware that contamination is present throughout The Journey of the Lubricant®. Taking small steps today, can help you run reliably and reduce the risk of equipment failure.
Get Help with Contamination
If you are interested in exploring how to identify your contamination threats, we can help you. We can quickly assess your current situation, provide recommendations, and help execute them.