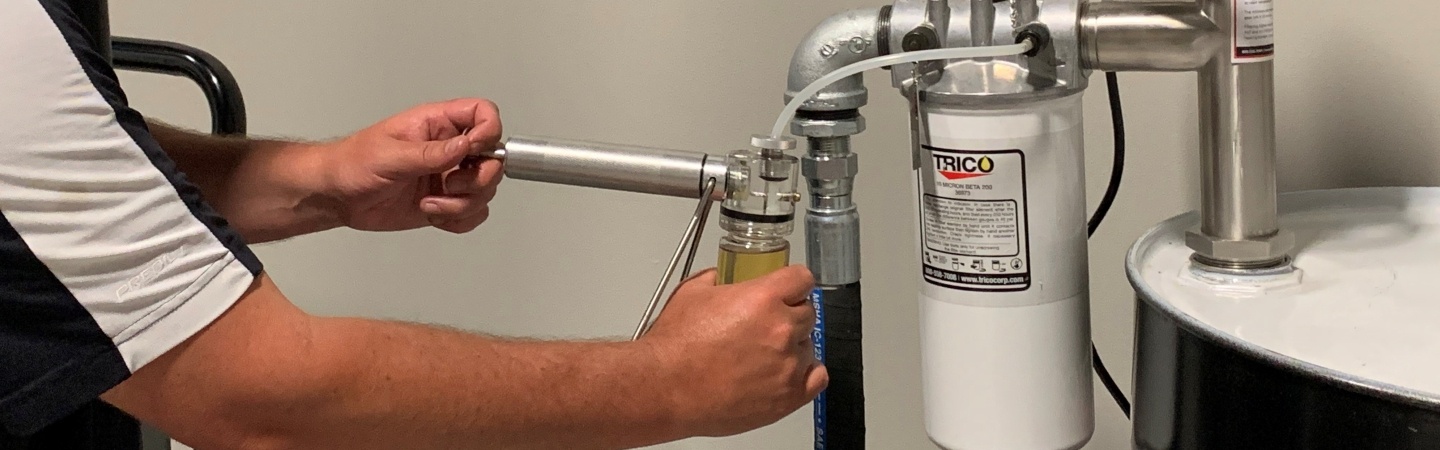
Mike Gauthier
08.04.2020
Obtaining representative, repeatable, and consistent oil sampling
Oil sampling is the most critical aspect of an oil analysis program. However, improper sampling procedures, inconsistent sampling locations, and the frequency of oil sampling can skew the oil analysis results. Some of the areas where data integrity could be comprised include:
- How was the sample taken?
- What tools were used to take the sample?
- Where was the sample taken?
- How was the sample handled from time of sample to the oil analysis technician?
All these areas need to be considered when extracting an oil sample. Your oil analysis results, and diagnosis is only as good as the quality of the oil sample. To maximize the effectiveness of your oil analysis program, oil sampling should be performed with the following goals in mind.
Maximize Data Density
Oil samples need to reflect the current operating condition of the lubricant and the equipment. Each oil sample carries a unique concentration of information related to the cleanliness of the oil, depletion of additives, and the presence of moisture and wear particles. These factors are compared against a baseline to determine the current condition of the equipment and lubricant. The more representative the sample is, the more accurate the diagnosis. Every oil sample must contain the maximum amount of data density it can – which is achieved by extracting the sample in the most appropriate place.
Minimize Data Disturbance
Oil samples should be extracted so that the concentration of information is uniform, consistent, and representative. It is important to make sure that the samples do not become contaminated during the sampling and handling process through dirty sampling ports, hardware, tubing, bottles and improper flushing. If they are not minimized it can distort the results. Procedures should be put into place to prevent the oil samples from becoming contaminated to minimize data disturbance.
Maximize Consistency/Frequency
Oil sampling consistency is important and should be repeatable. They need to be extracted in the same location, while equipment is in operation, if possible, using appropriate sampling hardware and procedures and at the same sampling frequency. One of the most powerful aspects of oil analysis is identifying a change in the baseline of an oil sample and understanding the rate at which the change has occurred. Setting up the appropriate sampling frequency and adhering to it will allow for sound decisions and the ability to plan maintenance activities.
Keep the Goals in Mind
Following these goals for oil sampling will result in a successful oil analysis program. A successful oil analysis program will extend mean time between failures, reduce downtime and loss of production, and provide you the opportunity to plan maintenance activities versus being reactive…which increases the bottom line.
Remember – The insights you gain from oil analysis are only as good as the samples you start with.
Want Some Help with Oil Sampling?
Do you want to make sure you get the right insights into contamination ingression and other issues? You can get support from Trico.
- Category:
- Oil Analysis
- Oil Sampling