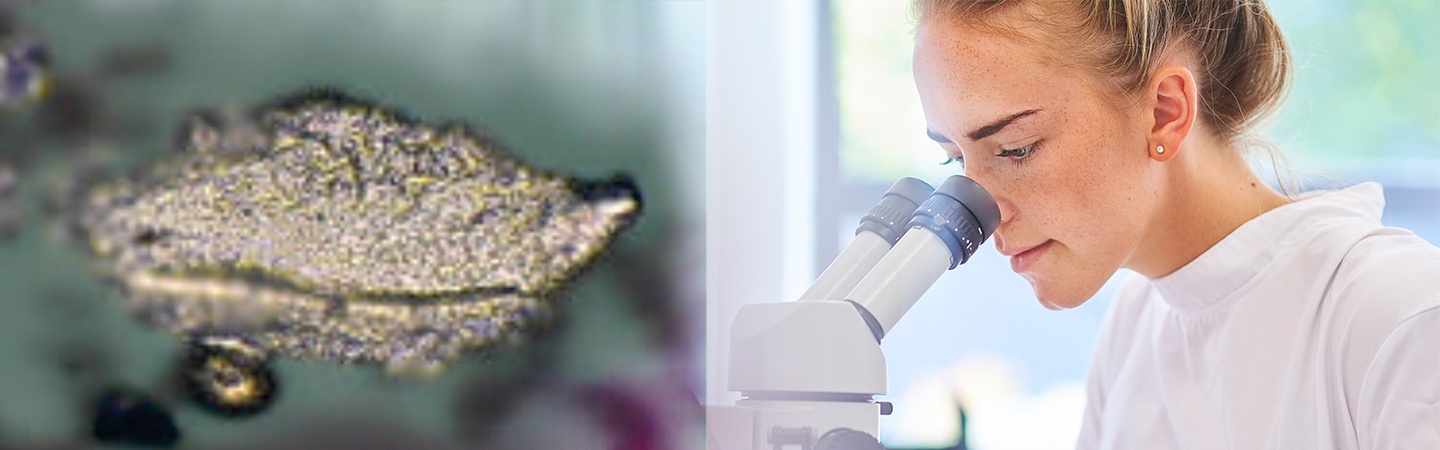
Victoria Bunchek
01.28.2020
Ferrography Proved Essential in Preventing Costly Downtime As Part of Comprehensive, Regular Analysis
By most measures, there was nothing wrong with the General Electric turbine generator at the petrochemical facility.
The standard in-house vibration analysis never showed anything amiss. Nor did routine tests including viscosity, water concentration, particle count and elemental analysis by Trico – with no indication of any wear or lubricant-related problems.
But then we did wear particle concentration testing via direct read ferrography, and the numbers came back high.
It’s a good thing, too, because as we later confirmed, a journal bearing in the generator had in fact entered a critical wear mode that could have cost the facility $100,000 or more.
This is one of many examples from our oil analysis records that illustrate the value of ferrographic analysis as part of a holistic and ongoing monitoring program for critical equipment lubricants.
Why Didn’t Standard Vibration Analysis or Elemental Analysis Help Identify the Problem?
The issue was subtle enough that standard vibration testing didn’t pick up on what was happening.
As for elemental analysis, this technique can identify many different elements by the bands of light produced when an oil sample is super-heated through inductively coupled plasma (ICP). Metallic elements such as iron, tin, copper, lead, aluminum, silver and nickel can be early indicators of machine wear.
However, ICP cannot read particles larger than 8 microns – which is a notable shortcoming because larger particles often are a sign of severe equipment damage. Elemental analysis through ICP didn’t detect the wear particles in this case because the particles turned out to be much bigger.
What Direct Read and Analytical Ferrography Found
As part of the regular oil analysis program for this equipment, the Trico team used a technique called direct read ferrography to determine wear particle concentration.
An oil sample is passed over magnets of varying strengths to trap ferrous (iron-based) materials of differing sizes. A light is then shined through the pile of material, and the amount of blocked light is measured as the amount of ferrous material.
This is the technique that showed unacceptable levels of wear particles in the sample. The next step was wear particle analysis through analytical ferrography, which involves taking a closer look under a microscope at any ferrous and non-ferrous particles of concern. This analysis helps distinguish types of wear that may be occurring (fatigue, adhesive, abrasive), as well as the material present (low, medium, high grade steel, fibers, rust, copper, etc.).
What we found was Babbitting material, which is an alloy coating of softer metals (lead, tin, copper) that protect a bearing and shell from wear. If this material goes, the bearing is soon threatened.
The size of the particles was 90 microns or larger, and quantity was rated moderate to high – indicating a critical wear mode was in progress and immediate maintenance was required.
After notifying the customer, they deployed a sophisticated vibration analysis technique called orbit plots to pinpoint and evaluate the problem bearing.
The journal bearing in question was rubbing against a non-rotating element, with too little lubricant film separation between the bearing and the shell, indicating a restricted or damaged bearing.
To make a long story short, they had to replace the bearing before suffering additional damage or downtime. And that’s exactly what they did – saving an estimated $100,000 in the process.
There are plenty of other examples like it – timely identification of wear particles that would have gone unnoticed if monitoring is limited to other techniques … or worse yet, no monitoring at all!
- Category:
- Oil Analysis
- Tags:
- Oil Analysis
- Wear Particles
Recent Posts
-
The Year of Lubrication Management
-
Oil Analysis in 8 Steps
-
Enhancing Industrial Safety
-
Lube Routes
-
How Machine Vitals Reduces the Impact of Labor Shortages on Maintenance
-
How Condition Monitoring Extends Equipment Lifespan
-
AI-Driven Maintenance
-
The Power of Temperature, Vibration, and Humidity Monitoring