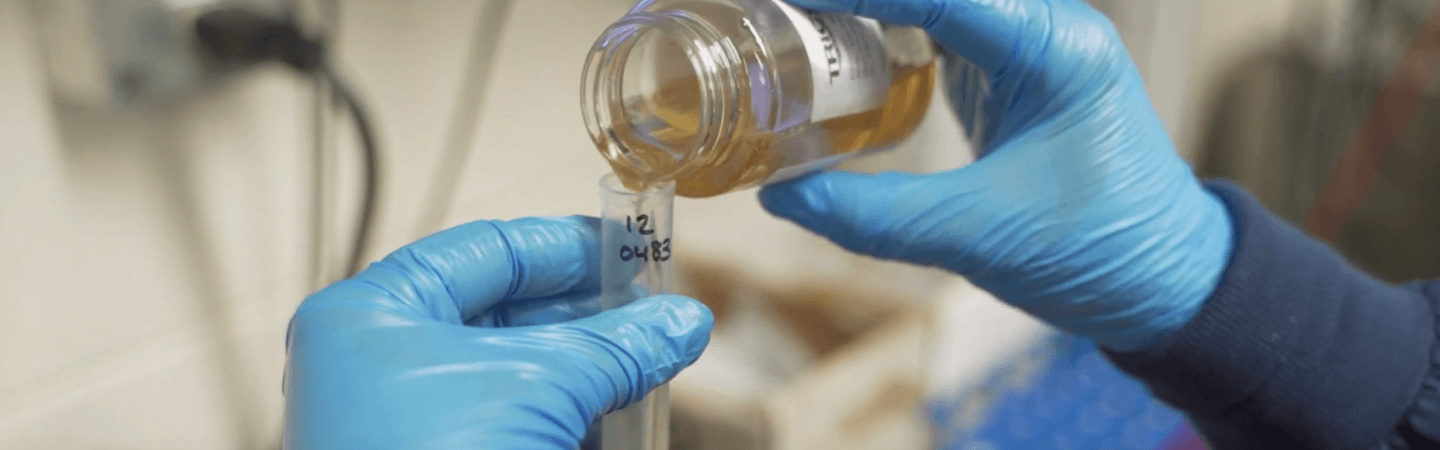.png)
Victoria Bunchek
04.04.2022
Using oil analysis to determine the root cause of equipment failure
A failure has occurred – hopefully not one that is catastrophic – but, now what?Even the best-run programs experience failure. The best thing that can be done is to learn from them and address the root cause of the issue so that the same failure does not occur again. Using oil analysis for Root Cause Failure Analysis is a powerful tool in understanding what may have led to the equipment problems. So, what exactly can you gain from testing the oil on a failed piece of equipment?
Was oil present?
This seems like a silly question but taking an oil sample can be a useful check for the most basic issue – without oil the components will wear quickly and may seize. Fix: Ensure that oil level can be monitored either physically or using technology like Sensei online monitoring tools.
Which components were affected?
Analytical ferrography can determine the metallurgy of components that were affected by the failure, and potentially the extent of the damage. Fix: Review the components that were damaged to ensure that they are replaced with the appropriate metallurgy to prevent premature wear
Was the right oil used?
By checking the chemistry of the lubricant including the viscosity and additives we can ensure that the right lubricant is applied – preventing premature wear and seizing Fix: The right oil must be applied to prevent wear. Consider color-coding storage and transfer containers as well as the equipment if this is a historical issue.
Was installation appropriate?
Using analytical ferrography can determine whether misalignment, soft-footing, or bearing over-tightening played a role in the failure. Fix: Your routine oil testing program should be catching these issues ahead of time, but make sure that when new equipment or components are installed that they are double-checked for these issues.
Was the load or speed a problem?
Severe sliding wear, when detected using analytical ferrography, can indicate that the components are shearing under heavy loads or high speeds. Fix: Adjust the operating conditions for the equipment, or work with the OEM to adjust the lubricant to meet the demands of operations.
Was water a problem?
Water is known to cause major problems for machinery. Determine the cause of the water and address it – process water? Coolant? Environment? These water types can have chemical signatures that can help identify the source of the issue. Fix: Address the root cause and then remove water with filtration and then keep it out with desiccant breathers if needed.
Did contamination play a role?
Contamination can come in many forms – process contamination, particulate from the environment, coolant, fuel, etc. Identifying if any of these played a role in the failure of your equipment can help you address future issues. Fix: Regular testing of the oil condition should identify contamination and wear conditions early enough to prevent damage through filtration, breathers, or oil changes.