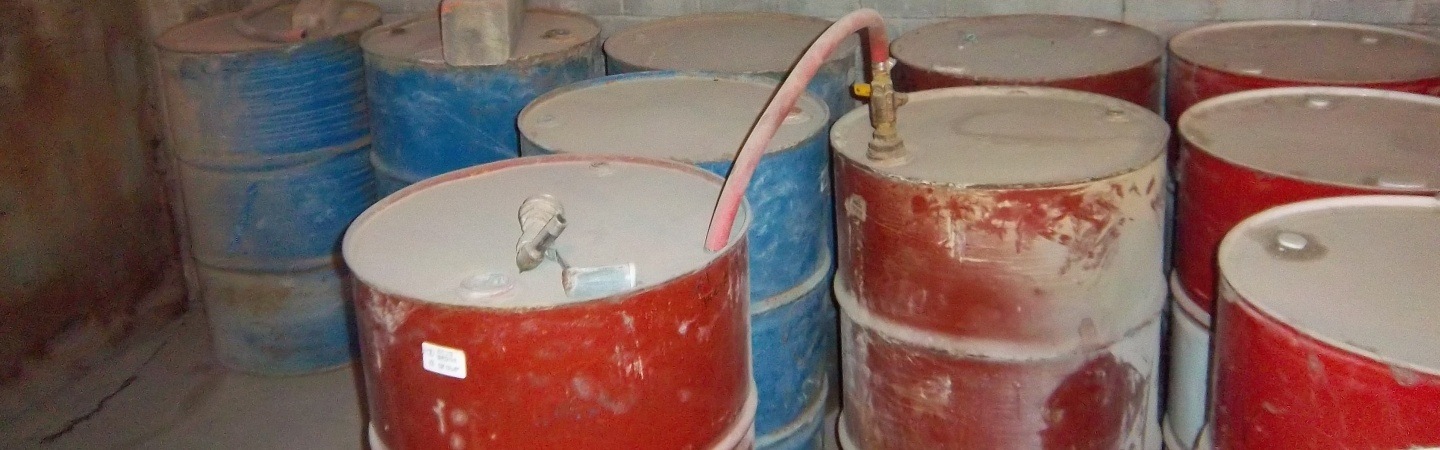.jpg)
Mike Gauthier
12.14.2021
Maintaining lubricant integrity with FIFO method
Over the years I have visited numerous facilities to help them with their lubrication/reliability programs. One of the biggest problems I always shake my head at is the storage and handling area. It is one of the more tangible elements of a great lubrication program, yet most have a tough time understanding its value. The “lube area” is some of the dirtiest areas of the plants I have been to. They are typically dark, dingy, and cluttered with 55-gallon drums and many items that don’t belong there. Because of this – I often ask the customer if they now which drum to use to top off their equipment. Most of them just shrug their shoulders.This is a problem. How do they know they are not using an outdated lubricant and that the lubricant is still good to use? Like many other items, lubricants do not last forever. If used past their useful shelf life, it can result in poor performance and potentially damage the components it is being used to lubricate.
What is FIFO?
Lubricants should be stored in way that makes it easy to rotate stock quickly. The best method for a stock rotation system is First In First Out (FIFO). FIFO means exactly what it sounds like. It is an inventory control method that ensures older lubricants are used before more recently delivered lubricants. This helps to prevent older lubricants from exceeding their useful shelf life. Understanding FIFO is similar to the service industry of “first come, first serve” – the FIFO system focuses on products (lubricant), not people.
Maintaining Lubricant Integrity
Most lubricants have a recommended shelf life to prevent deterioration of the product. Shelf life is not always available on the product, but it can be obtained from your supplier and/or manufacturer. When it comes to the shelf life of a lubricant it is based on the lubricant being stored in a clean, dry, and temperature-controlled area – not the “lube areas” I have seen. A lubricant’s longevity depends on how well you store and handle it. Below are a few factors that will help to maintain the lubricant’s integrity.
- Oil Analysis – Oil analysis validates the specifications of the oil as well as identifying contamination. The results will help determine next steps – whether the lubricant should be returned to the supplier or needs to be filtered.
- Date Stamping – Date stamping helps ensure the lubricant doesn’t exceed its useful shelf life. It is suggested to use custom labels that include manufactured date, receipt date, and date opened to facilitate FIFO method.
- Storage Location – Ideal location is to store oil drums indoors away from potential contamination and weather conditions.
- Temperature – Temperature variations will cause oil drums to breathe which will pull contaminants into the drum. Drums should be stored in area with a consistent room temperature of approximately 70ºF.
- Drum Bungs – Drum bungs need to be kept tightly sealed to prevent contaminant ingression. The use of desiccant breathers will help keep moisture and particles out.
- Storage Process – Drums should be stored horizontally on proper storage racks that facilitate FIFO
method with bungs at the 3 and 9 o’clock positions. This will prevent contaminants from entering the drum. The best practice in storage and handling is the use of bulk oil storage systems where oil is filtered from a 55-gallon drum to a 65 gallon tank in the storage system and filtered again before dispensing to the appropriate transfer container.
Get Help
If you are interested in exploring additional ways to improve your storage and handling practices, we can help you. We can quickly assess your current situation, provide recommendations, and help execute them.
- Category:
- Lubrication Program
- Storage