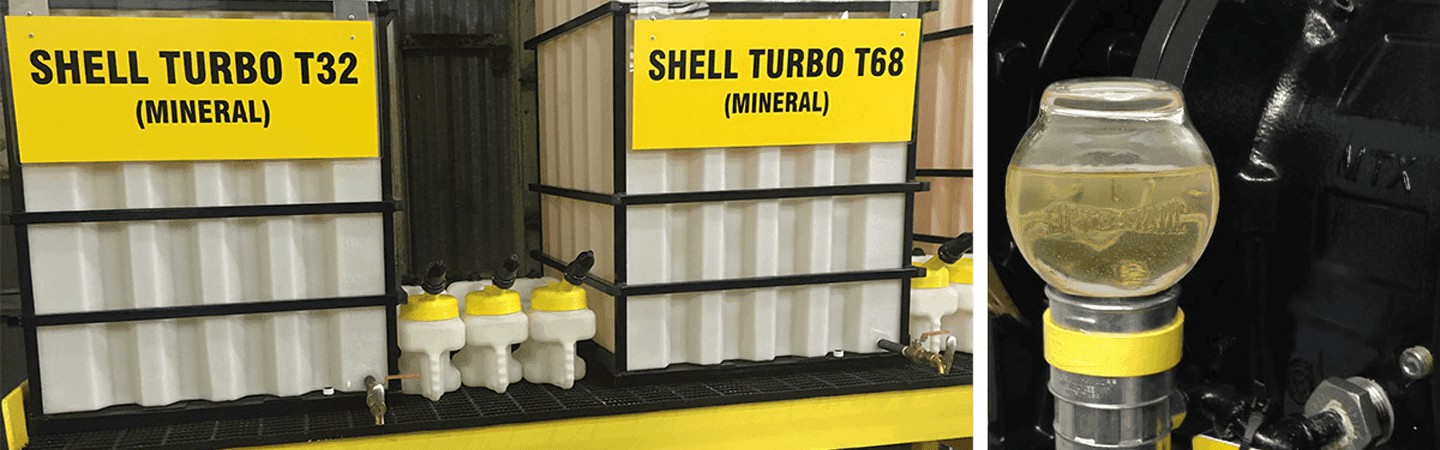
Jim Jung
11.12.2019
Start with These 6 Fundamentals to Get Your Equipment Lubrication Program Going
If you’re among the many industrial professionals who still view critical equipment lubricants as mere consumables – commodities to which you give little thought other than price – consider this: Poor lubrication causes as much as 60% of all equipment failures.
Just like your equipment, your lubricants should be treated as key assets. Lubricants have rights, too! To get you centered, here’s a quick overview of the six “rights” that are the foundation of an effective lubrication program.
- Right Product
It doesn’t matter how good a lubricant is if it’s not the right choice for your equipment.
There are many considerations, including the basic decision of whether you need a mineral or synthetic oil, plus different types of property-enhancing additives, depending on your application. To start with, the lubricants you choose should be based on original equipment manufacturer (OEM) recommendations, and you should continue to periodically review requirements with a qualified lubrication specialist. - Right Condition
Throughout a lubricant’s journey in your facility and its lifecycle in your equipment, oil analysis can be a highly effective tool in extending the useful life of your oil and the reliability of your equipment. Learn more about the Journey of the Lubricant®.
Monitor water and particulate contamination as well as additive depletion through regular oil analysis. To enhance protection, desiccant breathers are the best way to allow your equipment to breathe clean, dry air. Filtration systems also offer great advantages, considering the minimal upfront cost vs. potentially unlimited cost of unplanned failures – not to mention equipment life extension factors. - Right Location
Standard operating procedures (SOPs) are crucial to ensure all team members know where each machine should be lubricated.
Color-coded storage and organization systems should extend to these lubrication points, to minimize the risk of adding the wrong oil. - Right Amount
Too much or too little oil or grease can cause all kinds of problems. Fortunately, there are wonderful tools available to ensure proper amounts.
Constant level oilers, for example, provide a constant flow of lubricant in a small volume to achieve superior lubrication at a low cost in pump bearing housings, gearboxes or other oil sump applications. You can review options from Trico here.
For grease applications, single point lubricators and volumetric grease meters are excellent tools to ensure the proper amount of grease is being applied to components. These options can be reviewed here. - Right Time
When do you need to change the oil? Traditionally, it’s been done on a set interval as a precaution aimed at prevention. But oil analysis now allows us to take a more condition-based predictive approach to oil changes.
If you only perform maintenance procedures when you need to, based on data and science, you stand to save time and money. - Right Person
In many ways, the success of a lubrication program hinges on the personnel who are working with the products. They should be fully trained and ready to be lubrication champions who apply what they’ve learned on a daily basis.
Do you have defined roles for the personnel responsible for your program? Have your team members been trained on how to sample properly?
How to Get Right to It
These six rights provide the foundations of a world-class lubrication program. What’s next? An honest, thorough self-assessment of all these lubrication practices across your facility can be a powerful step toward reducing time, costs, stress and risks. If you’d like to get started, contact us to help you.