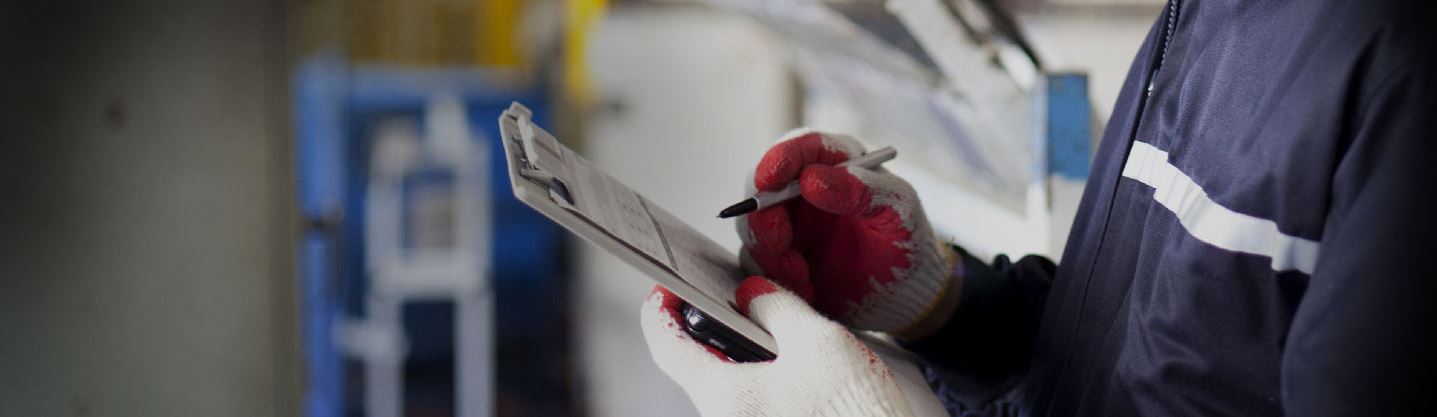
Victoria Bunchek
04.12.2019
Consider These Key Factors to Reveal More Valuable Oil Intelligence
So, you’ve noticed a problem with a lubricant in heavy-duty rotating equipment. A low oil level, say, or excessive water content.
You’re going to need to address that promptly, of course. But what’s the real issue?
It’s never just about that low level or water contamination. It’s always about many different factors acting together to lead to the current situation. Your issue is going to be closely related to multiple, ever-changing factors involving your process, your machine and your facility.
If you aren’t looking at all these factors beneath and beyond the surface – and many people don’t – you may only be treating a symptom, instead of diagnosing a bigger problem.
Here are the key considerations underlying any lubrication issue:
Conditions across your plant – What happens to your lubricant from the moment it’s delivered, through storage, transport and filtration, until it’s put into use?
In many facilities, the approach to these stages is haphazard at best. Add in your atmospheric elements – whether it’s outdoors during a cold winter or hot summer, or the plant itself is hot and humid – and you’ve got a recipe for problems with machine oil contamination or degradation.
The machine and the application – What are the specs for equipment you’re using and how you’re using it?
When examined by experienced eyes, equipment data that includes location within the plant and process, detailed technical specs, maintenance plan, operating schedule/throughput, etc., can be instrumental in zeroing in on the real issue.
Physical condition of the oil – Oil level, temperature, sight and smell – observations that may be your first indication that something’s amiss.
This info can be especially helpful if it’s compared regularly to a baseline over time. For example, an oiler that had the right amount of oil when checked for several weeks, but then was nearly out the next week, is going to raise a red flag.
Chemical condition of the oil – What’s inside the oil? Is it viable for your needs, or is there too much water or particulate contamination, too little additives or some other issue?
Regular oil sampling and analysis of lubricant from multiple points in your process will unveil the truth. However, getting to why an issue is happening and what you should do about it requires analyzing the data from an experienced vantage point, and in the context of the other key factors.
Applying These Insights to Oil Analysis for Critical Equipment
When we augment oil analysis by studying this whole picture – continuously cross-referencing and interpreting the relationships among multiple data points over time – we can uncover answers that make a real impact on your lubricants, your machines and your whole operation.
We call this more complete application of knowledge Oil Intelligence. Instead of just refilling the oil, or filtering out the water, maybe you can stop those problems from happening in the first place – and do something more productive with your time.
Recent Posts
-
Is Your Equipment’s Health Checkup Stuck in the Past?
-
The Pulp and Paper Industry in the Digital Era
-
The Fitness Tracker for Your Industrial Equipment
-
The Year of Lubrication Management
-
Oil Analysis in 8 Steps
-
Enhancing Industrial Safety
-
Lube Routes
-
How Machine Vitals Reduces the Impact of Labor Shortages on Maintenance