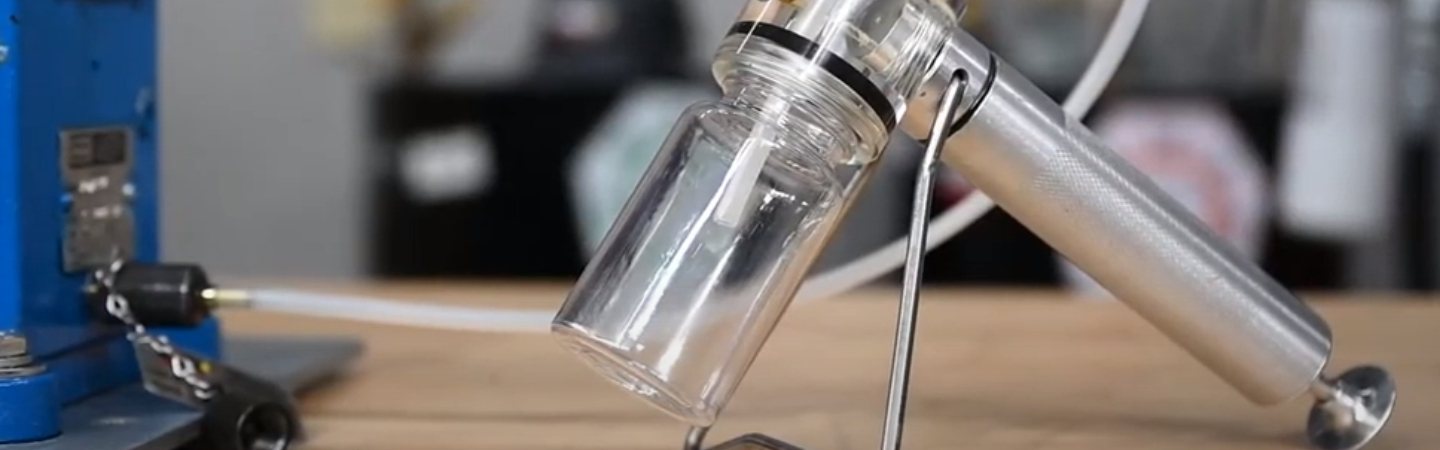.jpg)
Dan Freeland
05.24.2022
In statistics, dimensional sampling is a way of reducing the problem of sample size. But in the world of lubrication analysis, Trico has defined it in a way relative to your lubrication program, the Journey of the Lubricant®, and time. Lubricant contamination (water, particulate, cross-contamination) can occur anywhere along its lifecycle. Following the journey, dimensional sampling and oil analysis allows the ability to pinpoint weaknesses in your lubrication program based on comparing oil analysis results from the prior stage of the lubricants life. It also provides a “chain of custody” relating to the quality of your lubricants at each stage.
Oil sampling and analysis at “Arrival” provides indication of the condition and care your supplier has taken to ensure lubricant meets specifications and is contaminant free. Oil analysis at this stage is essential from a forensic standpoint. Without a reference sample, diagnosing problems later in The Journey of the Lubricant becomes more difficult because there will be more variables to eliminate.
Regardless of the storage containers you use, periodic oil samples are required to assure lubricant integrity is maintained. Sampling at this stage identifies how your practices are impacting your lubricant condition. Oil analysis will provide the information you need to make decisions like whether to filter your oil or improve your storage methods. Lubricants can stay in this stage for extended periods of time. Performing dimensional sampling on a time schedule basis maintains oil quality chain and the chain of custody until transfer takes place.
This is the stage where lubricants are taken from primary storage containers to secondary, color-coded, containers. Primary containers should incorporate filtration when dispensing into secondary containers. Take your sample from the secondary container as oil is being introduced to the equipment. This provides the best baseline for equipment test results. Any oil changes from storage to transfer is often affected by personnel interactions. Using disposable funnels into the point of use will eliminate additional contaminants when filling.
Oil sampling and analysis in the application stage offers the earliest warnings of wear and helps detect detrimental contamination. Sample oil from equipment on a schedule to track oil and equipment health. To achieve best sampling results and reduce man hours, set up your equipment to take proper oil samples with pitot tubes and sampling ports. This should be scheduled when equipment is down for PM or repair.
The lifecycle stage is the “working” life of your lubricant. From the time it enters your equipment until the end of its useful life and disposed of. Effective maintenance programs incorporate on-going, routine oil analysis, and data trending for continuous improvements.
Arrival Stage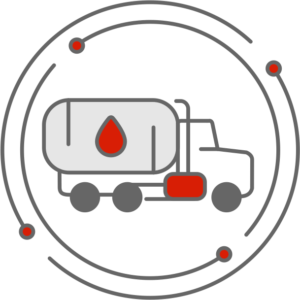.png)
Oil sampling and analysis at “Arrival” provides indication of the condition and care your supplier has taken to ensure lubricant meets specifications and is contaminant free. Oil analysis at this stage is essential from a forensic standpoint. Without a reference sample, diagnosing problems later in The Journey of the Lubricant becomes more difficult because there will be more variables to eliminate.
Storage Stage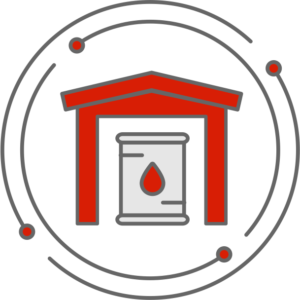
Regardless of the storage containers you use, periodic oil samples are required to assure lubricant integrity is maintained. Sampling at this stage identifies how your practices are impacting your lubricant condition. Oil analysis will provide the information you need to make decisions like whether to filter your oil or improve your storage methods. Lubricants can stay in this stage for extended periods of time. Performing dimensional sampling on a time schedule basis maintains oil quality chain and the chain of custody until transfer takes place.
Transfer Stage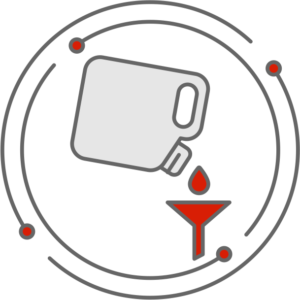
This is the stage where lubricants are taken from primary storage containers to secondary, color-coded, containers. Primary containers should incorporate filtration when dispensing into secondary containers. Take your sample from the secondary container as oil is being introduced to the equipment. This provides the best baseline for equipment test results. Any oil changes from storage to transfer is often affected by personnel interactions. Using disposable funnels into the point of use will eliminate additional contaminants when filling.
Application Stage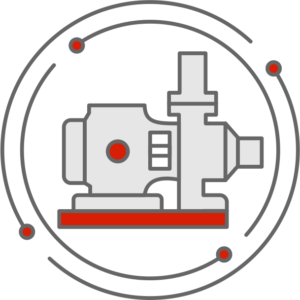
Oil sampling and analysis in the application stage offers the earliest warnings of wear and helps detect detrimental contamination. Sample oil from equipment on a schedule to track oil and equipment health. To achieve best sampling results and reduce man hours, set up your equipment to take proper oil samples with pitot tubes and sampling ports. This should be scheduled when equipment is down for PM or repair.
Lifecycle Stage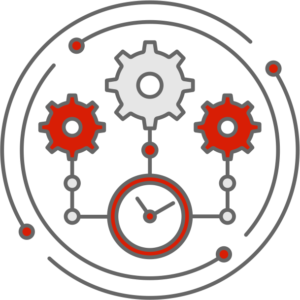
The lifecycle stage is the “working” life of your lubricant. From the time it enters your equipment until the end of its useful life and disposed of. Effective maintenance programs incorporate on-going, routine oil analysis, and data trending for continuous improvements.
- Continuous review EQUIPMENT conditions based on trends and results in:
- Direct Read Ferrography (DR)
- Elemental analysis (ICP)
- Analytical Ferrography (WPA)
- Continuous review LUBRICANT conditions based on trends and results in:
- Viscosity or Viscosity Index (VI)
- Karl Fischer (KF)
- Elemental Analysis (ICP)
- Fourier-Transform Infrared Spectroscopy (FTIR)
- Particle Count (ISO PC)
Creating a Chain of Custody
Keeping a chain of custody approach of the condition and quality of your lubricant at each stage of the Journey of the Lubricant can transform your approach to your lubrication program. Dimensional Sampling will jump start your program to move from Reactive Maintenance to Preventative and Predictive Maintenance. Learn more on oil sampling by watching our short video.- Tags: