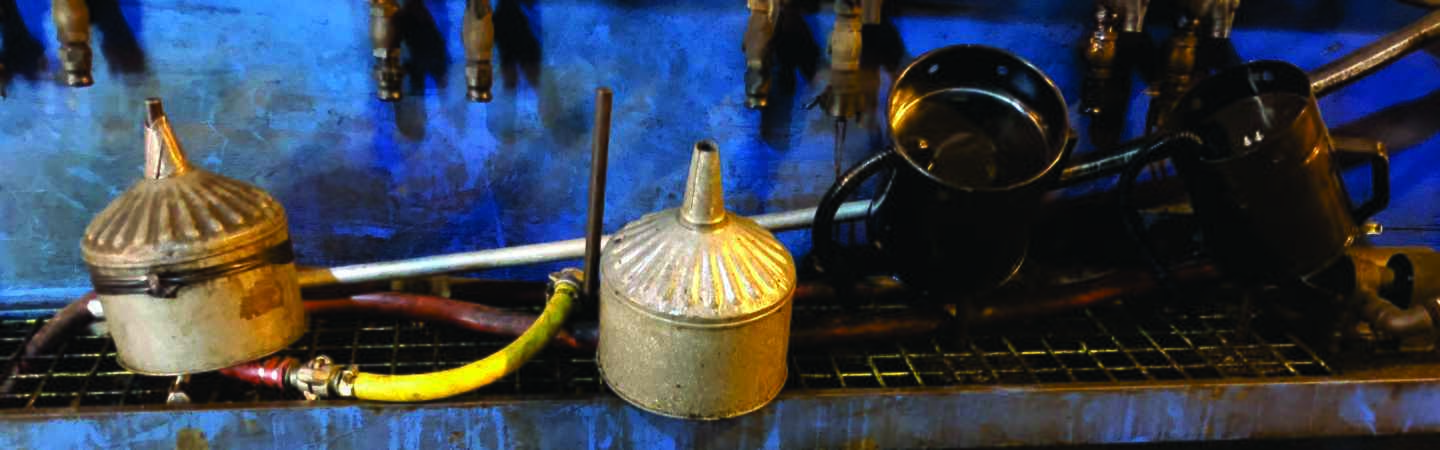.jpg)
Lisa Kiepert
08.09.2022
Contamination control is critical to the life of your equipment
There are many points in the lubrication management process that contaminate oils, at the blending facility, in transfer to the distributor, and even at your own site. Monitoring the health of the lubricant is an important part of your lubrication program that begins when lubricants arrive and continues throughout the Journey of the Lubricant®.
Refineries, Suppliers, Distributors
Before oil is delivered to your facility it goes through a rigorous process at the refinery that includes multiple transfers from one machine to another including multiple containers, which allows the oil to collect contaminants along the way. For example, if the refinery’s tanks and pipelines are not clean it can potentially add contaminants to the new oil.At the refinery, the lubricant is stored in large tanks and is then transferred several more times through piping and pumps before it is transported in a tanker truck to a lubricant supplier or distributor. The large tankers used for transfer should be routinely cleaned but they too can add contaminants to the new oil you receive.
When the new oil is delivered to the distributors’ location, it is transferred again with more pumps through more pipes into smaller oil drums, bulk packaging, and other tanker trucks shipped to their final destination. Each step of the way creates opportunities for contamination of your new oil before it reaches your facility.
Unfortunately, there isn’t a lot that can be done to prevent oil contamination at the manufacturers’ or distributors’ site. However, if there is a contract or purchasing agreement in place and the volume of purchased oil is sufficient, minimum standards can be created and integrated into the contract that indicates and specifies minimum cleanliness standards for new oil deliveries. This enables you to reject new oil deliveries if it is grossly contaminated. It is recommended that you analyze your oil when it is new so that you have a baseline for performance and machine health. Bear in mind that the criteria shouldn’t be too narrow to cause the cost to be prohibitive. This will allow you to audit the oil and perform analysis on bulk shipments to determine the extent of the contamination and then any necessary filtration needed to meet your expectations for use.
Onsite Practices
As we’ve discussed new oil can enter your facility with built-in contaminants, but that’s just the beginning. Some lubrication management practices create additional opportunities for contaminants to enter your machines and cause catastrophic failures including top-up practices and storage procedures.There are a variety items and practices that can add contaminants to your oil like, hand crank pumps, unclean funnels, dirty containers, reservoirs, and other oil vessels.
Dirty funnels are a source of contamination which should be handled with care. Reusable funnels should be stored in a dust free environment and cleaned properly before and after each use. Disposable funnels should also be stored in a dust free environment and properly disposed of after use. Best practice top-up procedures would include oil transfer containers that feature a spout and container that can accommodate an extension to access hard to reach areas.
Hand-crank pumps installed on top of oil drums are an example of poor practice. They allow large amounts of wear particles like moisture, dust, dirt, and other airborne debris to enter the drum from the loose clearances due to inexpensive mass production techniques. They also, don’t have a filtration system to allow you to filter the oil before it is transferred to the machine.
There are a variety of oil storage systems which incorporate filtration solutions offering best practice oil storage procedures that are convenient and relatively inexpensive. A few solutions to ensure that new oil is clean is a drum pump on your 55-gallon drums to dispense directly from the drum into the transfer container. And filter carts with kidney loop filters allows bulk oil to be filtered as its being transferred into a transfer container or storage container.
The most effective way to control the ingression of contaminants is to store your lubricants in a well-designed, fully functional permanent bulk oil storage system. These storage systems allow you to filter lubricants to reduce particulate and moisture contamination prior to adding to the machine. Desiccant breathers are included to remove moisture during storage.
There are many plants that still use galvanized tin oil containers, plastic water jugs, coffee cans, and even soap or bleach bottles to store and transfer oil. Open containers allow anything in the environment to enter the oil, including anything that remains in the container from its original intended use. To help prevent contamination, use only approved, dedicated oil transfer systems with lids that seal out any environmental contaminants that could potentially enter the container. The ideal storage and transfer configuration would include a color-coded system allowing for the use of a plant-wide color coordinated system dedicated to each lubricant to reduce cross contamination. The color-coded system can be extended to the actual lubrication point to identify which lubricant goes precisely into a specific lubricated component.
A lubrication program should include standardized procedures or tasks to provide consistency and accuracy related to lubrication storage, handling, flushing, topping-up procedures as well as cleaning pumps, reservoirs, gearboxes, and other sumps. A procedural document should detail the safety requirements, tools required, and specific steps to perform the task properly. These documents ensure that the tasks are performed in the same manner each time providing consistency while ensuring the task is performed properly and safely.
Reduce Contamination
Contamination control is critical to the life of your machines and longevity of your oils. By making a few modifications to your existing lubrication management practices, you can save your machines by reducing avoidable contaminant ingression.Need help in assessing your needs for contamination control. Contact us we are more than happy to help.