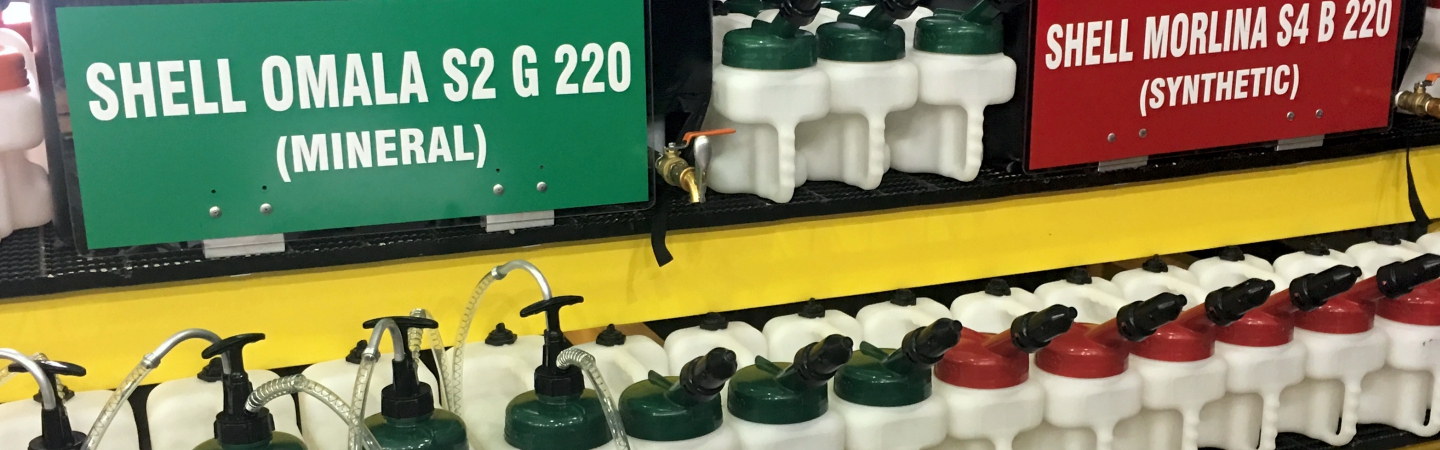
Mike Gauthier
06.09.2020
Implementing a Color-Coded System in Your Lubrication Process
Did you know that color is processed by people before they are consciously aware of it?
Color helps communicate essential information that is understood universally, requires little training, and transcends language barriers.
In fact, you probably already make use of color in your facility to one degree or another – to identify pipes (water, gas), electrical wiring, and locations of danger (such as paint or tape on floors).
Color can be used to improve maintenance practices by removing guesswork, simplifying tasks, reducing human error, eliminating cross-contamination, and preventing misapplication during the lubrication process.
Ease and Simplicity Throughout the Journey of the Lubricant®
The concept is straightforward, everything that the lubricant encounters during its Journey is marked with a color that corresponds to that designated lubricant. This means all drums, storage containers, dispensers, transfer containers, lubrication points, etc. have the same color identifier. Employees can easily see which items are used with which lubricant and where each lubricant should be applied. Following the Journey of the Lubricant from arrival to application is as easy as connecting the dots – colors.
Note: Approximately 7% of males and 1% of females are color blind. Incorporating shapes and/or numbers to the color-coded system is an effective way to incorporate those who cannot distinguish between different colors.
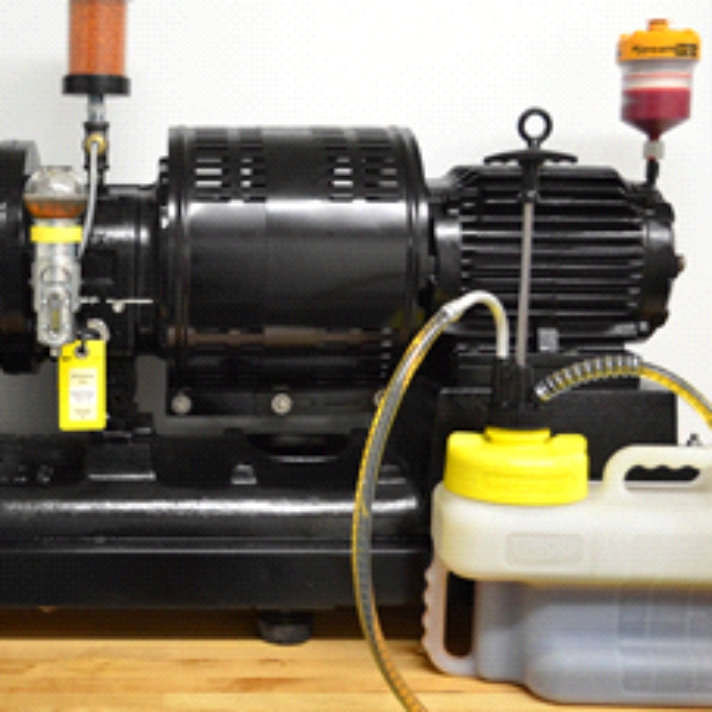
What’s the Purpose of Color-Coding?
In most facilities, lubricants are handled by a variety of employees (with different responsibilities) and in a variety of locations throughout the Journey. A color-coded system assists in helping employees understand the Journey of the Lubricant and removes the guesswork from the lubrication process.
- Eliminate Cross-Contamination
A color-coded system protects the quality of your lubricants throughout its Journey. A system is designed so that each drum, dispenser, and transfer container touches only one of type of lubricant – doing so prevents problems caused by cross-contamination. - Prevent Lubricant Misapplication
Utilizing a color-coded system is so intuitive it helps employees apply the “Right Product” to the “Right Location” correctly, keeping your machines up and running. - Reduce Human Error
Color-coding simplifies the lubrication process, removing the confusion and guesswork that can slow down technicians.