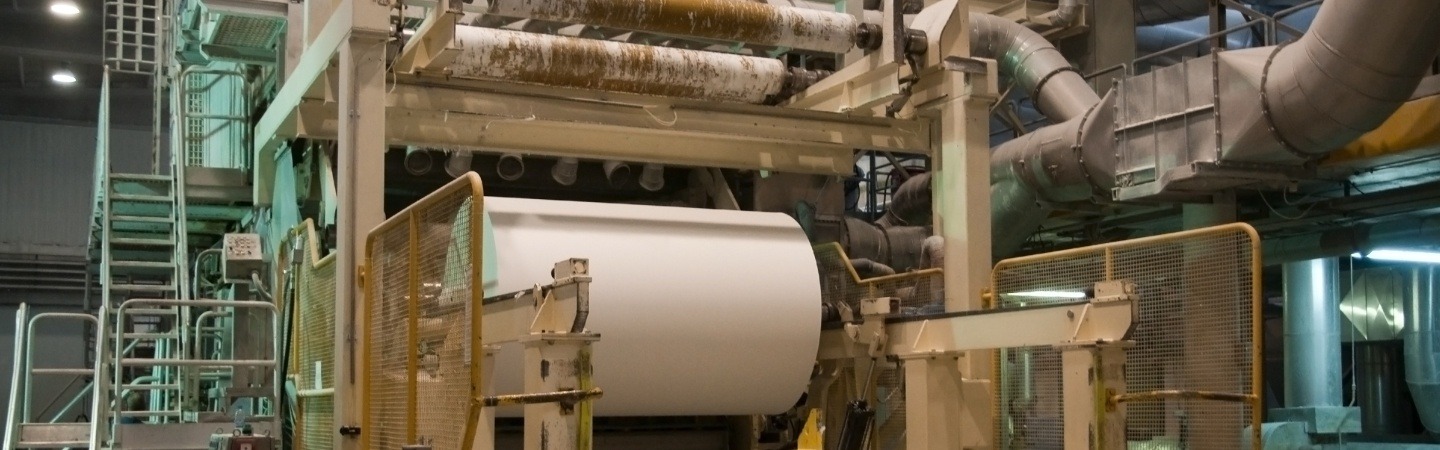.jpg)
Mike Gauthier
11.01.2022
Papermaker saves $500,000 from an audit
“Audit” can be a scary word for some, but it doesn’t have to be!When we hear the word “Audit” we think of an IRS audit, however I’m talking about a machinery lubrication audit. This type of audit can provide you with a substantial amount of savings instead of you owing money.
That’s exactly what Trico did during the first day of a 3-day machinery lubrication audit where we helped a papermaker client uncover a problem that cost them more than $500,000 a year in repairs.
Problem
The company was running ISO VG 220 weight oil through its centrifugal pumps. The appropriate oil should have been ISO VG 68. In other words, the company was using three times the viscosity required. This means many things to a manufacturing company – all of them bad. Pumps using such heavy oils are forced to pull more amperage to operate. This causes greater wear and tear, hotter operating temperatures, increased friction and vibration. Inferior operating efficiencies and dramatically reduced equipment life spans are the result.
Actually, this kind of problem isn’t uncommon. During client audits, Trico found 40% of all machinery assessed to have the wrong lubricant. One audit showed 80% of machinery to be using the wrong oil.
Maintenance managers are incredibly busy putting out fires all day long. There just is not a lot of time to apply the proactive steps required in a machinery maintenance program.
On top of that, they may be working with faulty information that has been passed down through the generations. One maintenance manager substitutes an incorrect lubricant for the correct one. Maybe it’s a temporary fix that becomes part of the routine. Nobody catches it and you’ve got a big problem.
Solution
In this case, after discovering the wrong lubricant was applied to roughly 300 pumps throughout the mill, Trico recommended an immediate solution. An analysis of the oil requirements for each piece of equipment was made. At that point, Trico recommended proper viscosity grades for each machine. To extend further, we used visual identifiers (colored tags) on the equipment at each lubrication point to identify which lubricant type and viscosity goes into a specific lubricated component. These serve as a confirmation check for the lube techs. In addition, these visual identifiers were used in the company’s storage area and transfer containers, using a plant-wide coordinated color system dedicated to each lubricant.