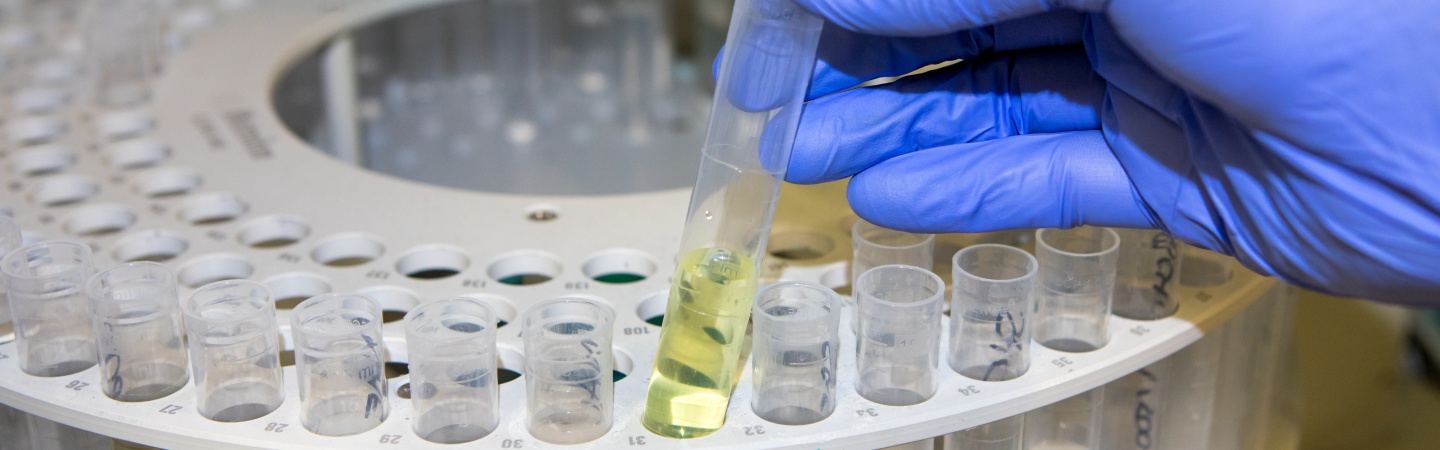
Lisa Kiepert
07.23.2024
Understanding Industry Priorities for Optimal Equipment Performance
The importance of oil analysis cannot be overstated when it comes to machinery maintenance. To gain insights into what professionals consider the most critical aspect of oil analysis, a recent poll was conducted on LinkedIn, posing the question: "Which aspect of oil analysis do you find most crucial for maintaining machinery health?" The results provide a fascinating glimpse into industry priorities.
Poll Results:
1. Contamination Detection: 47%2. Wear Metals Monitoring: 13%
3. Additive Depletion: 20%
4. Viscosity Testing: 20%
Contamination Detection: Leading the Pack
Unsurprisingly, contamination detection emerged as the top priority, garnering 47% of the votes. Contaminants such as dirt, water, and other foreign particles can wreak havoc on machinery, leading to increased wear, reduced efficiency, and ultimately, costly downtime. By regularly monitoring for contaminants, maintenance teams can take proactive measures to prevent damage and extend the life of their equipment.
Wear Metals Monitoring: A Vital Yet Undervalued Component
Although wear metals monitoring received only 13% of the votes, its importance should not be underestimated. Tracking the presence of wear metals in oil samples helps identify internal component degradation before it leads to significant failures. This early detection allows for timely maintenance and replacements, ensuring machinery operates smoothly and reliably.
Additive Depletion and Viscosity Testing: Equal Importance
Both additive depletion and viscosity testing received 20% of the votes, reflecting their equal importance in the eyes of industry professionals. Additives in lubricants play a crucial role in preventing oxidation, corrosion, and wear. Monitoring their levels ensures the oil maintains its protective properties. Meanwhile, viscosity testing ensures that the oil maintains its correct thickness, providing adequate lubrication and reducing the risk of mechanical wear.
The Integral Role of Oil Analysis
Oil analysis serves as the lifeline of machinery and lubricant health. By examining various parameters, maintenance teams can gain invaluable insights into the condition of both the oil and the machinery it lubricates. Each aspect of oil analysis—contamination detection, wear metals monitoring, additive depletion, and viscosity testing—provides unique and critical information. The emphasis placed on each aspect will vary depending on the specific needs and priorities of the machinery in question.The results of the LinkedIn poll underscore the multifaceted nature of oil analysis. While contamination detection is deemed most crucial by a significant margin, the other aspects remain vital components of a comprehensive maintenance strategy. By leveraging the insights provided by oil analysis, maintenance teams can enhance equipment reliability, reduce downtime, and achieve optimal performance.
Want to start an oil analysis program or review your current one, let us help you.