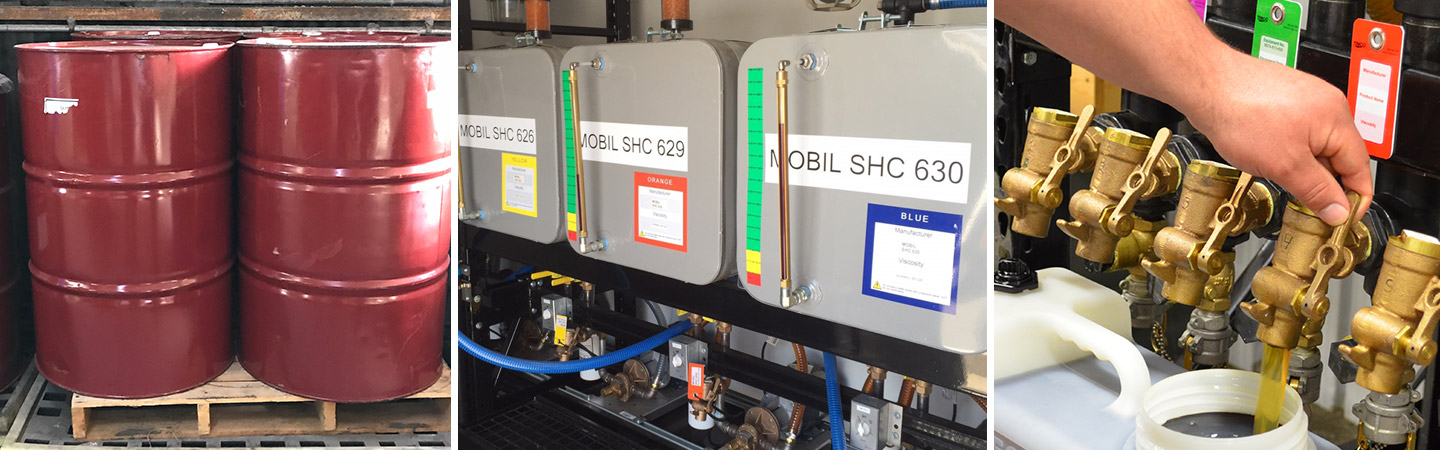
Victoria Bunchek
12.12.2019
Here’s Why and When You Should Take Reference Samples of Lubricants Before They’re Put into Service
Prevention, as they say, is better than the cure.
This is the number-one reason for taking what are called reference samples of oil before you put it into your system. These samples are essential to:
- Address any issues prior to causing a problem in your process.
- Understand initial conditions and water and particle concentrations, so that changes in samples of used oil from equipment are more readily apparent.
Instead of taking these samples, why can’t you just rely on the data from your oil supplier?
Because suppliers, as a rule, don’t provide all the available data about each of their oils. For example, there are proprietary additives and concentrations that are not otherwise published for comparison, so you need to test for them at your lab. In addition, formulations can change from time to time without notice to customers.
Perhaps most crucially, as we discussed in a previous post, poor storage and handling practices at your oil supplier can dramatically impact oil quality.
If you ever change vendors, taking a reference sample on arrival should be your first step.
Assuming you agree that this benchmarking is valuable, the question remains as to when you should take your reference samples. You have a choice of taking a sample from any of three distinct stages of The Journey of the Lubricant®.
Each stage, however, has benefits and drawbacks. So let’s explore your options and help you determine the most effective approach.
Arrival Reference Samples
Oil samples taken on arrival provide the best representation of what you were just sold from your vendor and what their practices have been to preserve the quality of the product.
Unfortunately, we find that 61% of lubrication professionals do not sample or test new oil upon receipt.
You should! If nothing else, the results of the analysis can back you up in a discussion with your supplier about their practices and your expectations. Don’t expect much in return if you’re dissatisfied, though; many vendors tack on exuberant upcharges for oil that meets certain quality standards like ISO particle count.
So what is the downside to taking reference samples on arrival?
If you’ve purchased a three-month supply, that leaves 90 days for condition changes before the last of that oil gets put into service. Changes might include chemical reactions without any human interaction, like hydrolysis. Not evaluating the initial quality leaves you guessing later about when these issues really occurred.
Storage Reference Samples
Sampling from storage can help identify how your practices are impacting your oil.
It can also provide a better picture of the condition of the oil that’s going into your system. But the accuracy of this picture can vary by your practices, such as sampling from open barrels or using the same drum pump across different lubricants, which exposes the oil to cross contamination risks or airborne particulate.
Maybe you doubt these issues could arise in your facility because you run a tight ship. But our experience has shown us that even in the most well run operations, mistakes and careless behaviors happen.
Still, the question is, when during storage should you take samples? If you’re taking a sample each time a new barrel is opened, it’s hard to isolate the impacts of what your maintenance personnel are doing or the impact of environmental factors.
You may not be able to perfectly and capture all storage variables, but if you’re consistent in how and when you take samples at this stage, you’ll help reveal the truth over time.
Transfer Reference Samples
Sampling during oil transfer may give you the best indication of the condition of the lubricant you’re putting into your system – especially to compare with used oil samples coming out of that system.
But transfer is also the most volatile and variable stage of the journey.
Not much looks worse than the containers used for transferring oil we see at most plants. Plastic Sunkist and Coca-Cola bottles seem to be especially popular. They don’t start out clean, and they get touched and mishandled from there, leaving plenty of room to compromise oil condition.
However, a sample at this stage doesn’t necessarily identify where problems begin. The oil is already well on its way through the Journey within your facility, and could easily have gone awry in lots of ways.
So if you want to have a frank discussion with your oil supplier about the condition of the oil they’re providing, this isn’t the sample to do it with. As soon as you tell them where this sample came from, they’re going to point the finger at you.
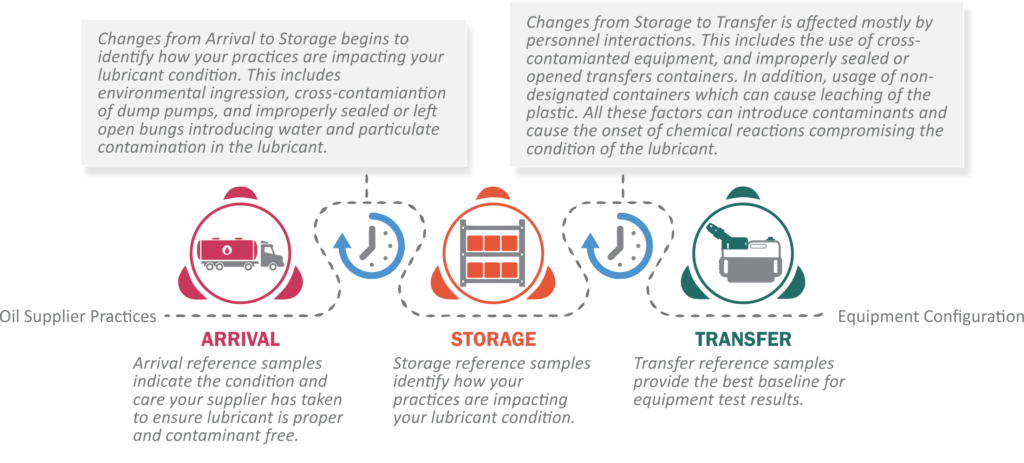
When You Should Take Reference Samples
What we’re telling you here is all these reference sample locations are great and terrible at the same time. So what do you do?
The correct answer is to take reference samples from all three stages each time you supply references – roughly every six months, corresponding with the delivery that occurs closest to that interval. This frequency will help normalize the data at each sample stage, getting rid of unrepresentative outliers.
Reference samples at all three stages allow you to see the impact of your storage and handling practices and enhance your understanding of the samples coming out of your equipment – what they reveal about performance and reliability of your setup.
Here’s what our reference sample recommendations boil down to:
- When new oil arrives, take a sample immediately.
- Go to any open barrel of the same lubricant and take another sample.
- If you have any oil sitting in a transfer container, take that as well. If you don’t have any oil sitting in a transfer container, pump some into whatever is commonly used for transfer and then pour or dispense it into a sample bottle.
The key is to be as consistent as possible with what your normal practices are, which will help you put a stop to problems before they ever take root in your system.
By the way, in 2020, if you use Trico Corporation as your lab, you’ll see all three reference samples on your condition reports and portal analytics.